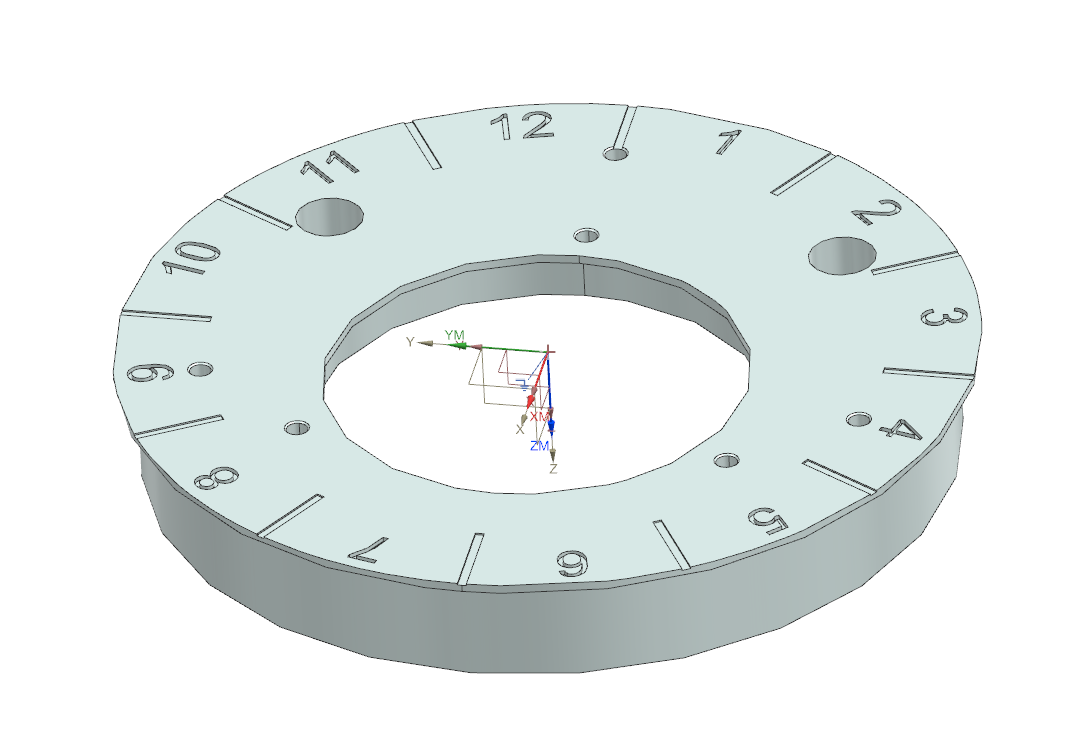
These eccentrics allow us to adjust chain tension easily.

NX CAM preview
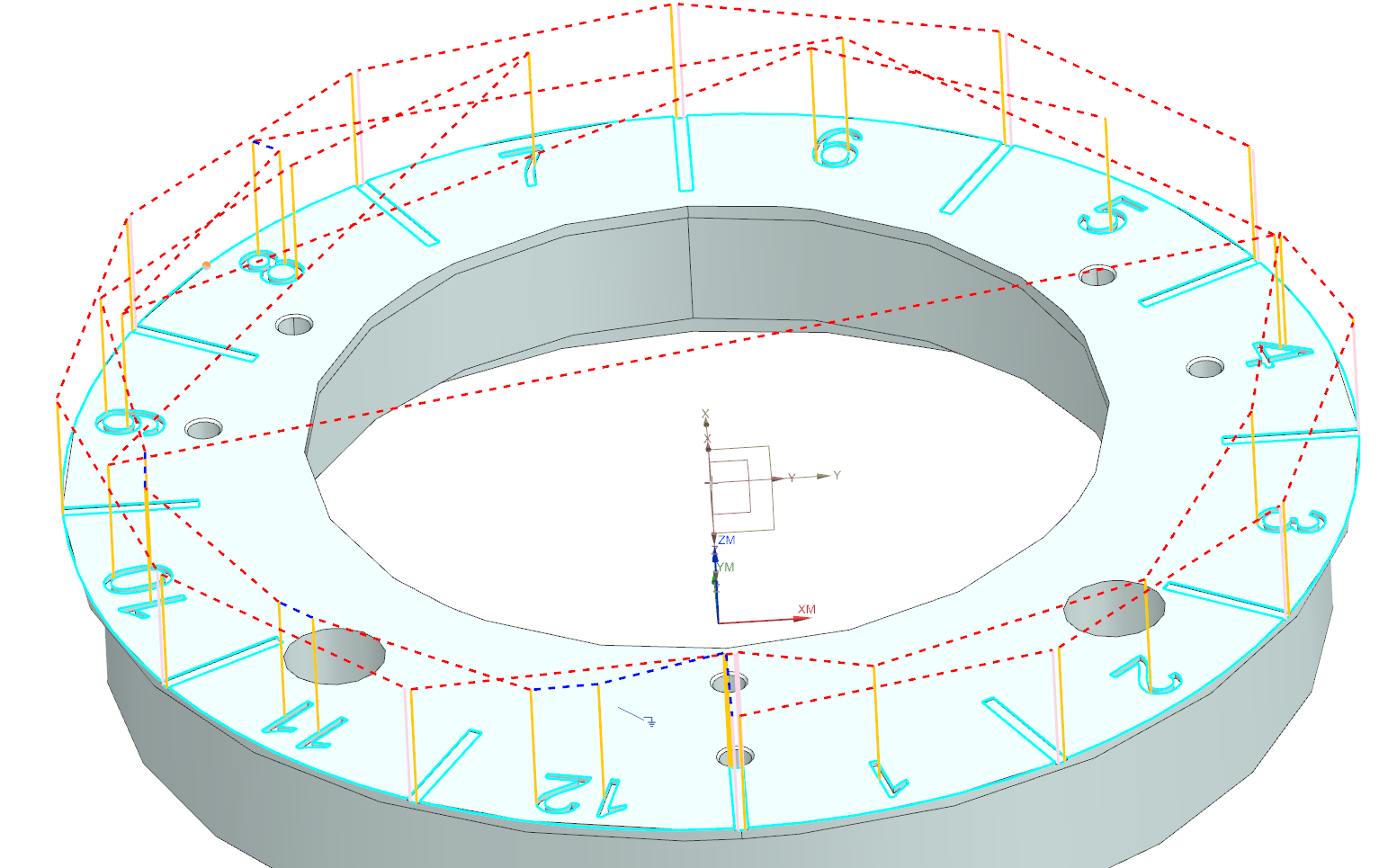
The second operation.
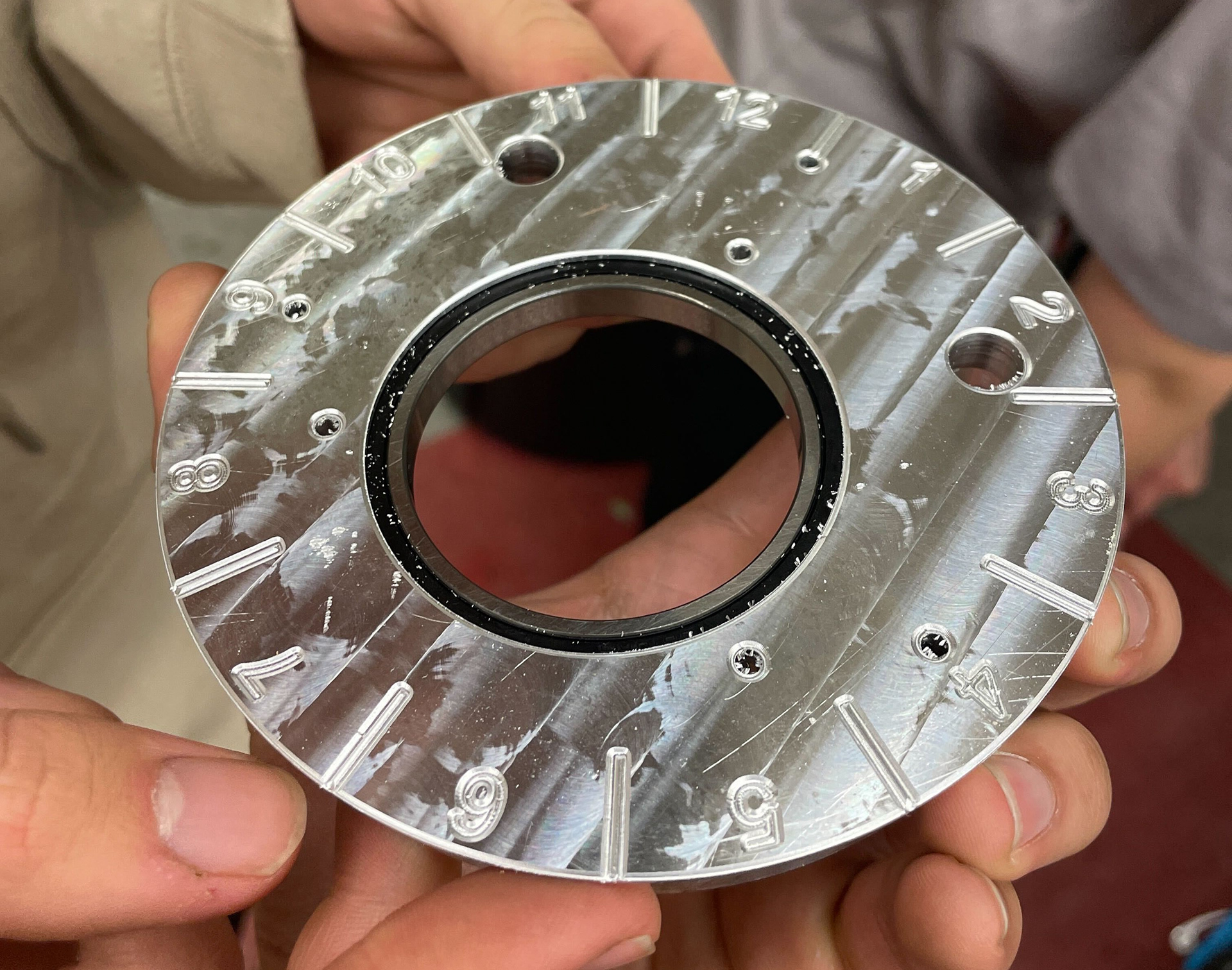
The bearing press-fit hole was dialed in .001 inches at a time.
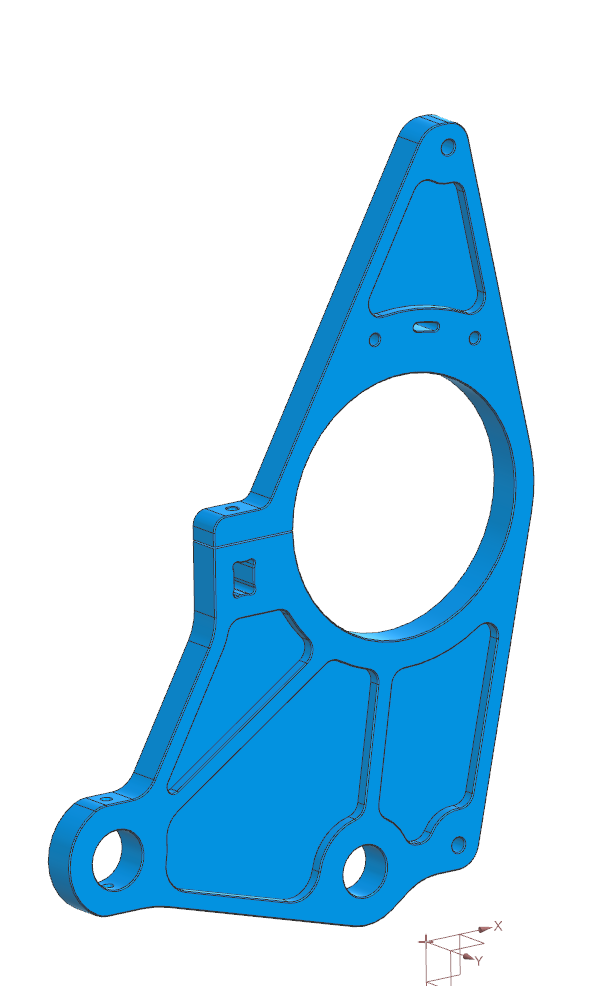
This plate attaches the differential to the car frame via the eccentrics.
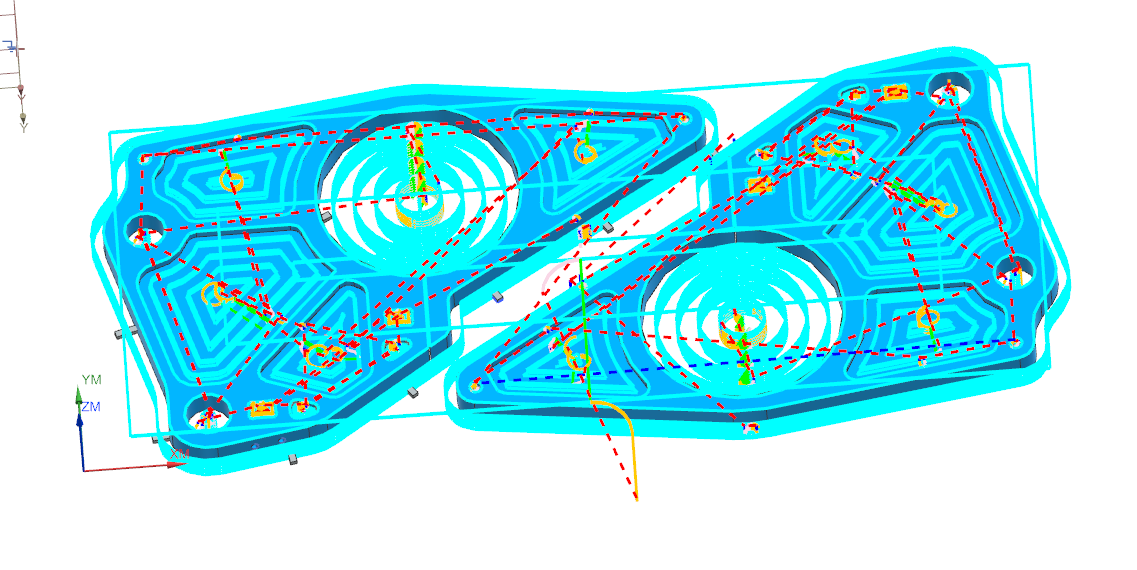
Each hole had to be precisely dialed in .001" at a time for precise slip and press fits.
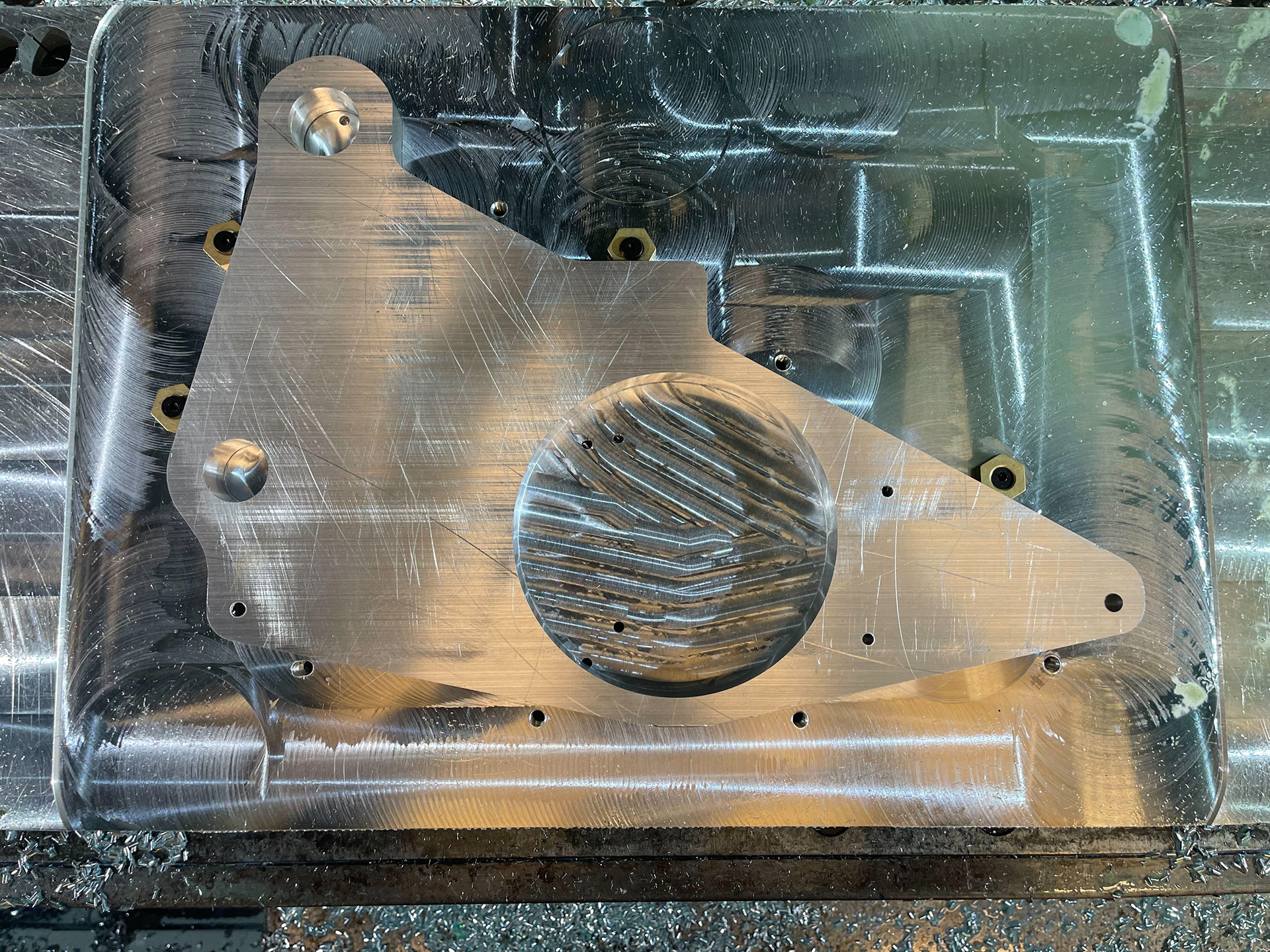
I created a custom jig to locate the plate for the second operation precisely. This jig was a perfect slip-fit for the plate.
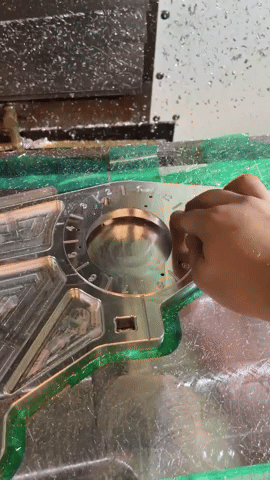
Perfect slipfit!
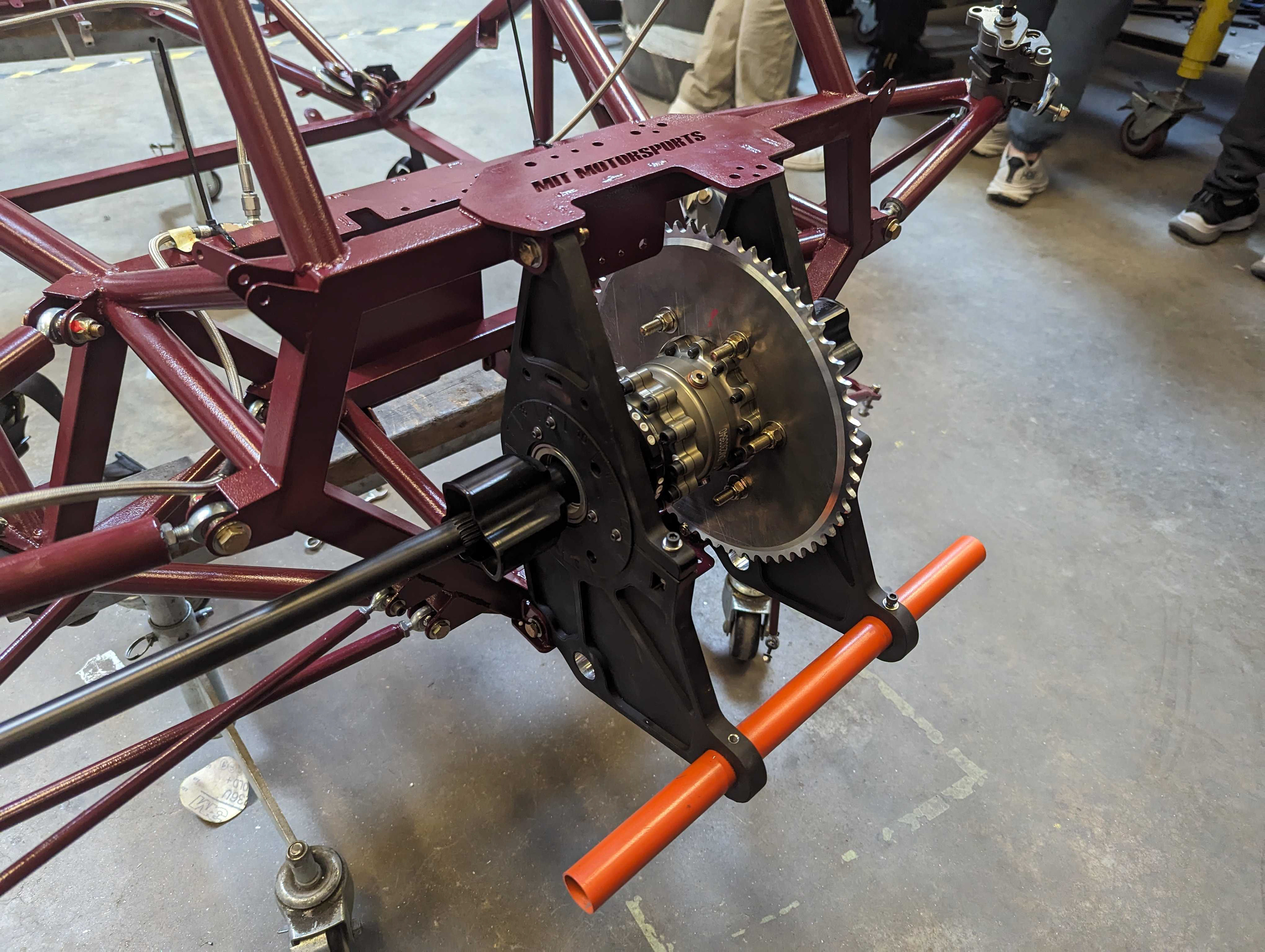
The Eccentrics and differential plates on the car post anodization.
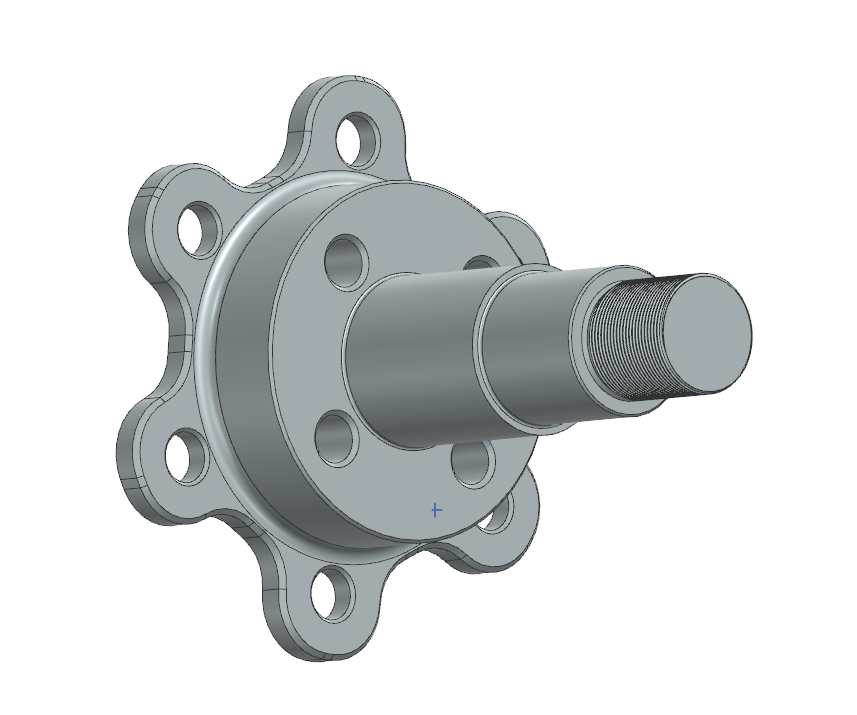
The motor hub allowed us to attach a sprocket to the motor as well as support it.
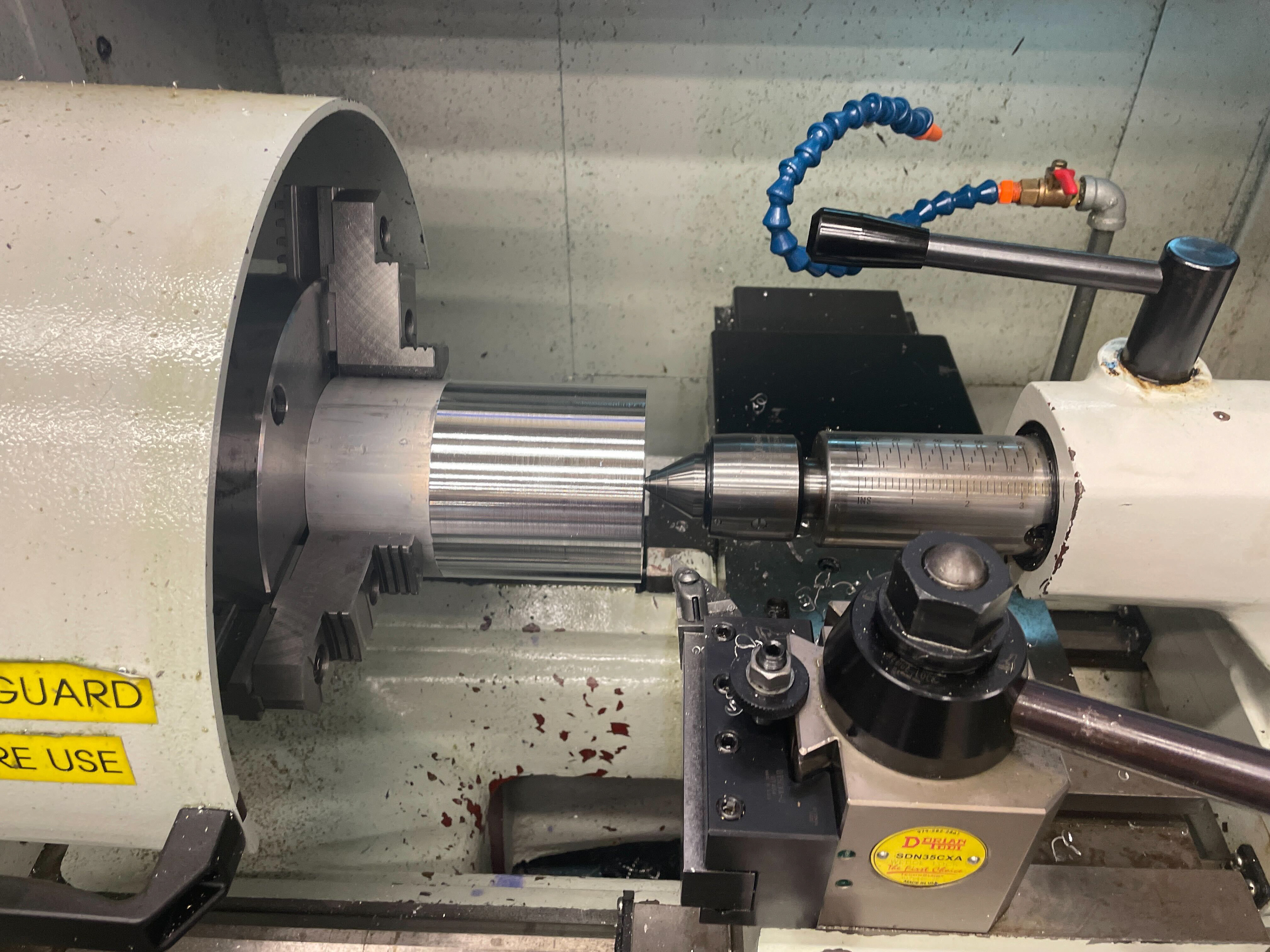
I did the first operation on a manual lathe.
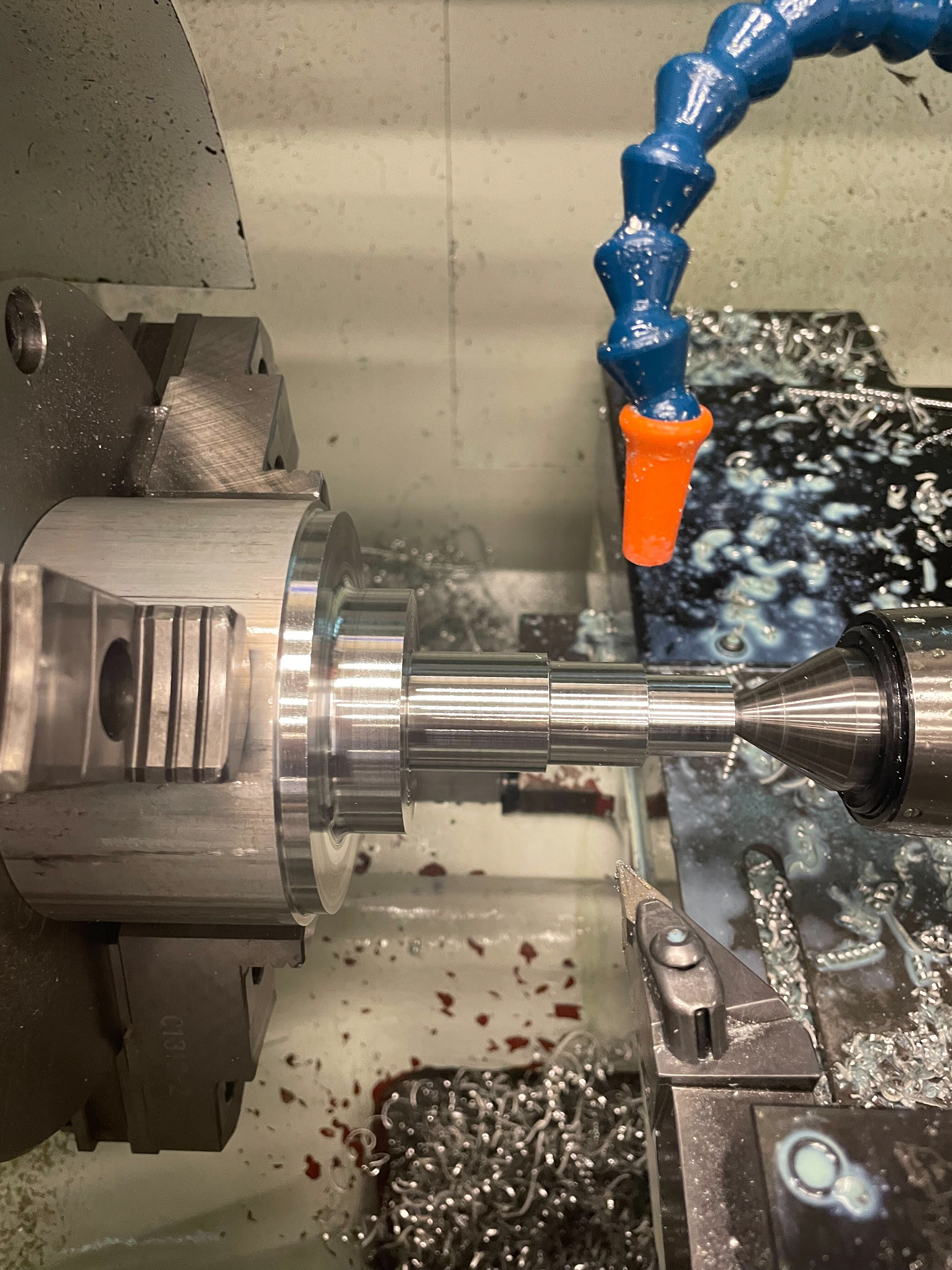
Intermediate state, ready for finishing.
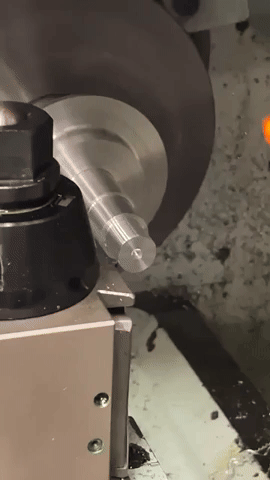
Single point threading a .781"-32 thread.

Bearing and sprocket surfaces were dialed in to be perfect slip fits.
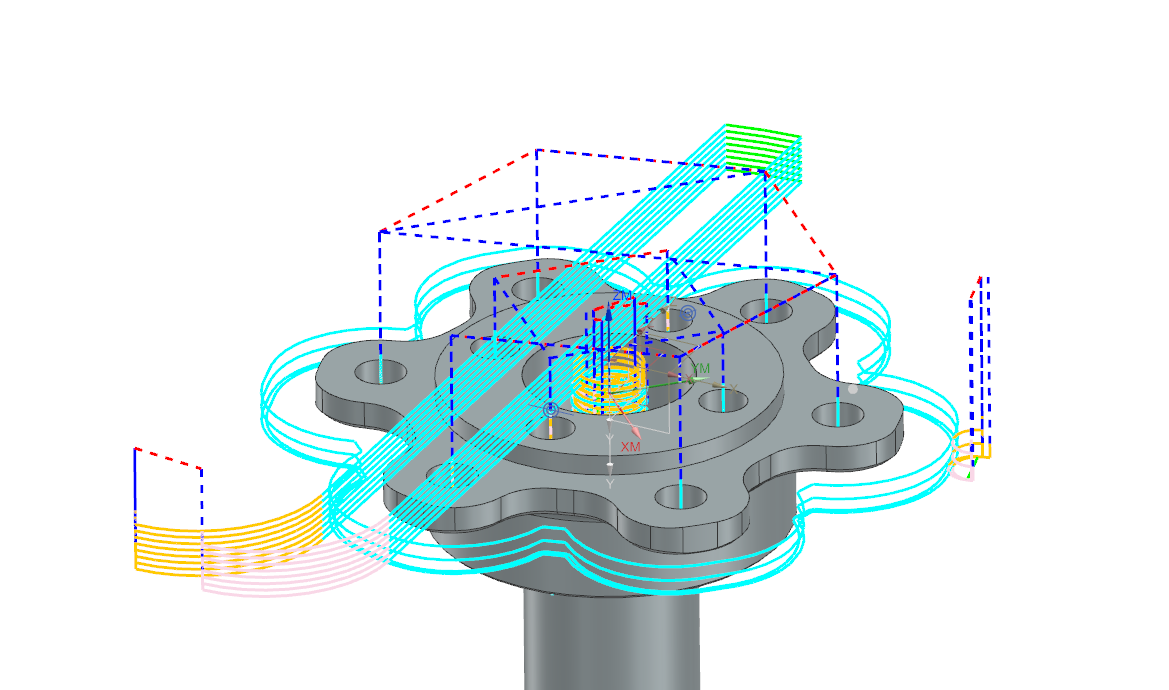
Second operation was done on the VF2.
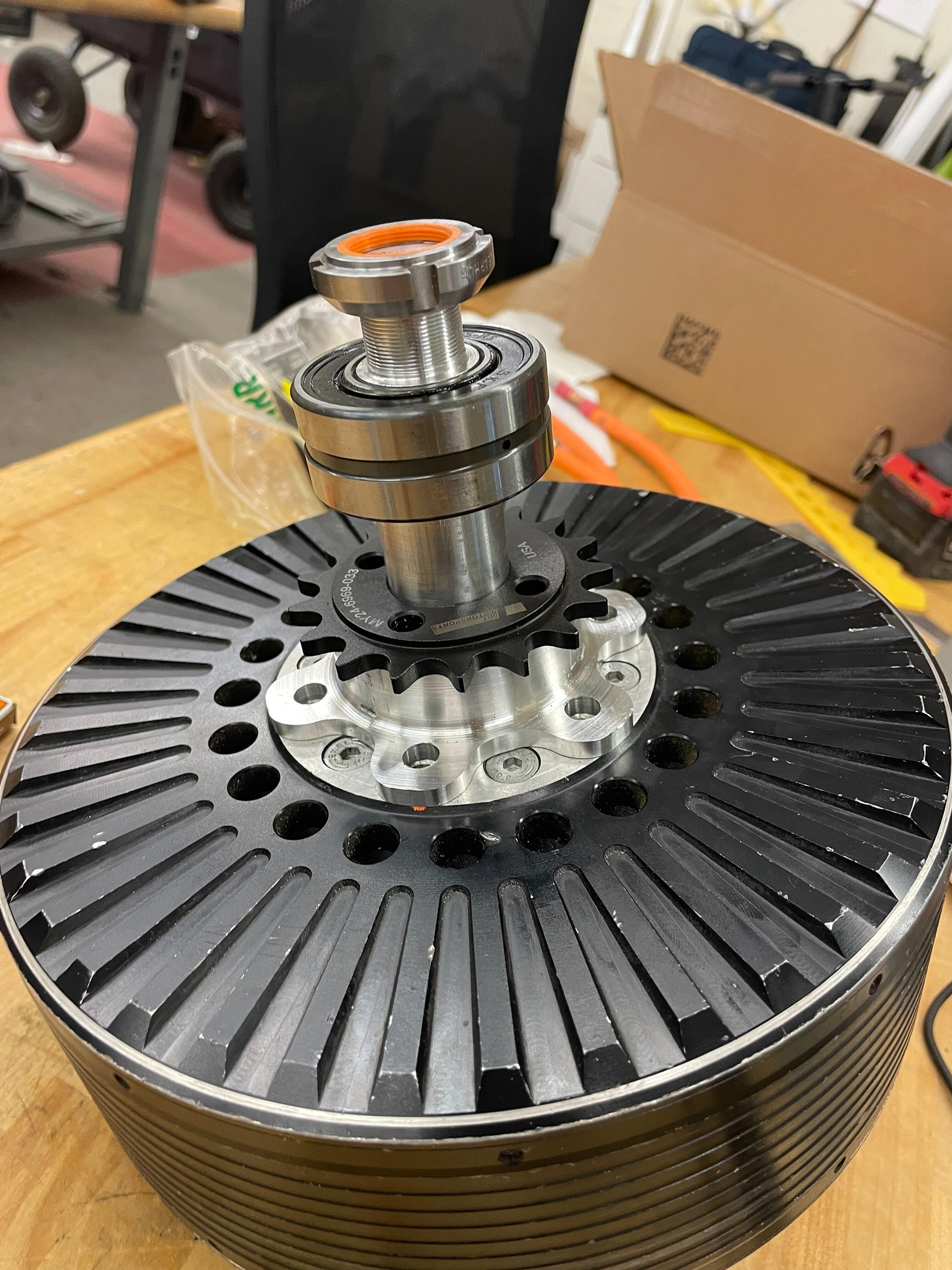
Final part on the motor.