To better understand how the MY25 Wheel Hub will behave under load, I utilized Siemens NX Pre/Post in conjunction with NASTRAN. This model also helped me check the results of my hand calculations.
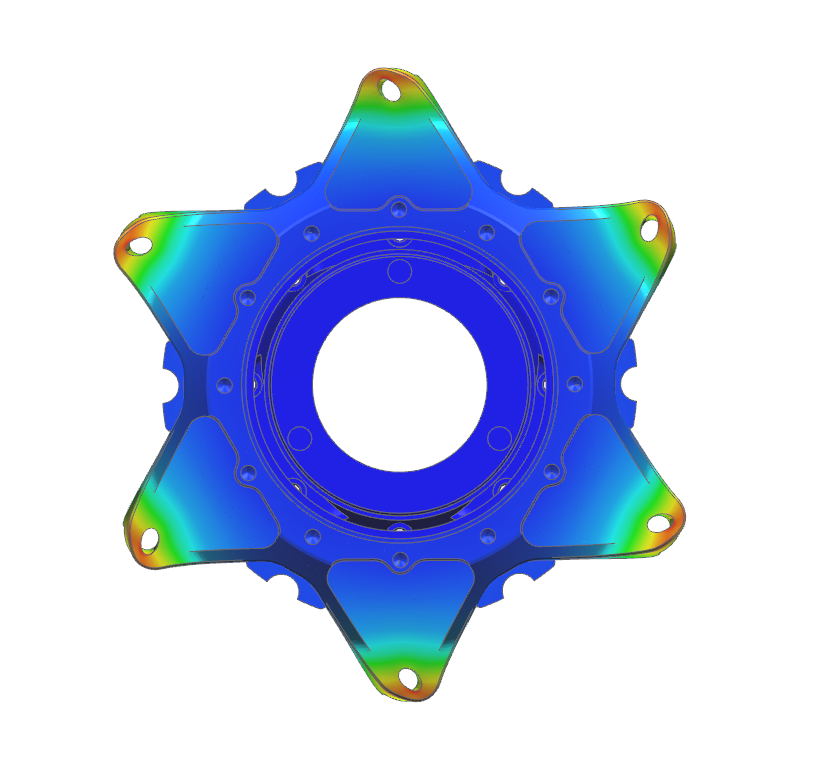
One of the Hub's Resonance Modes
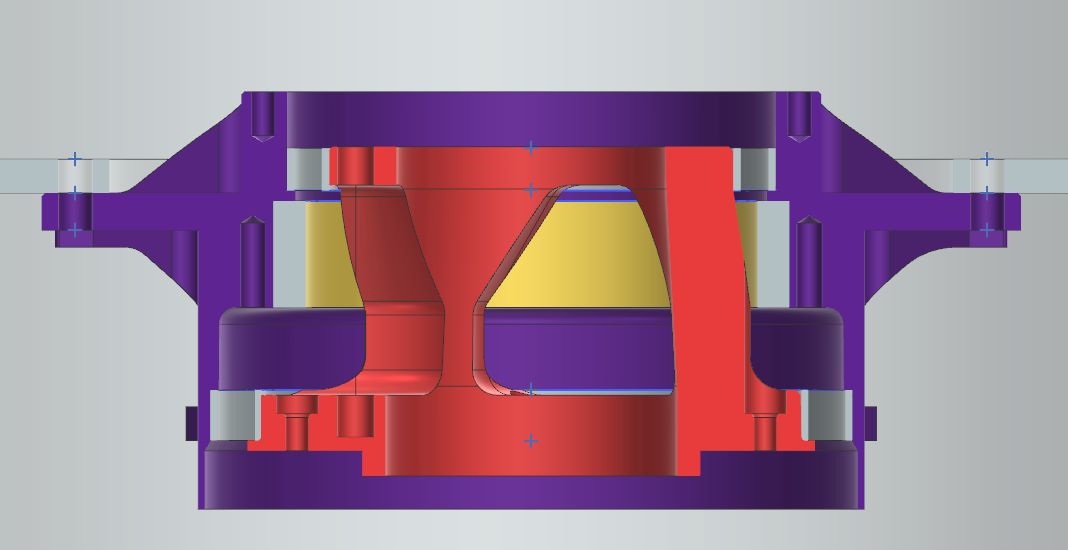
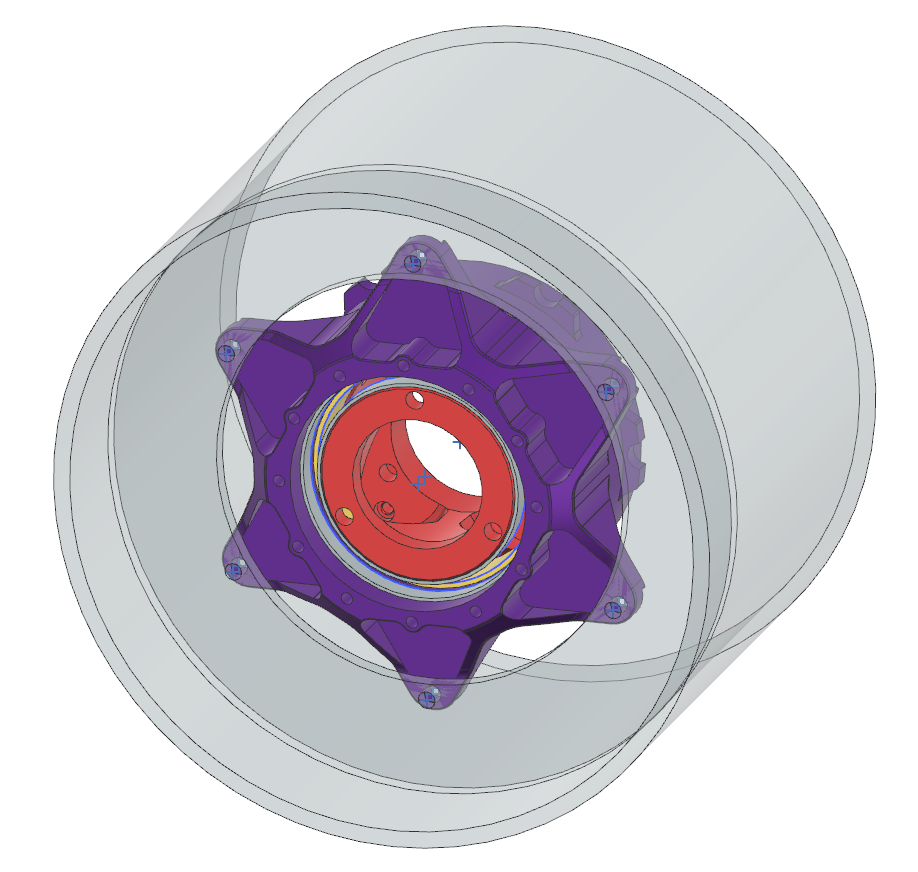
First, a simplified model of the hub was created, deleting small chamfers and fillets that can create artificial stress concentrations. This model also includes a simplified gear carrier, bearings, and rim, to which forces and constraints will be applied. Additionally, points are created for later connections in the meshing process.

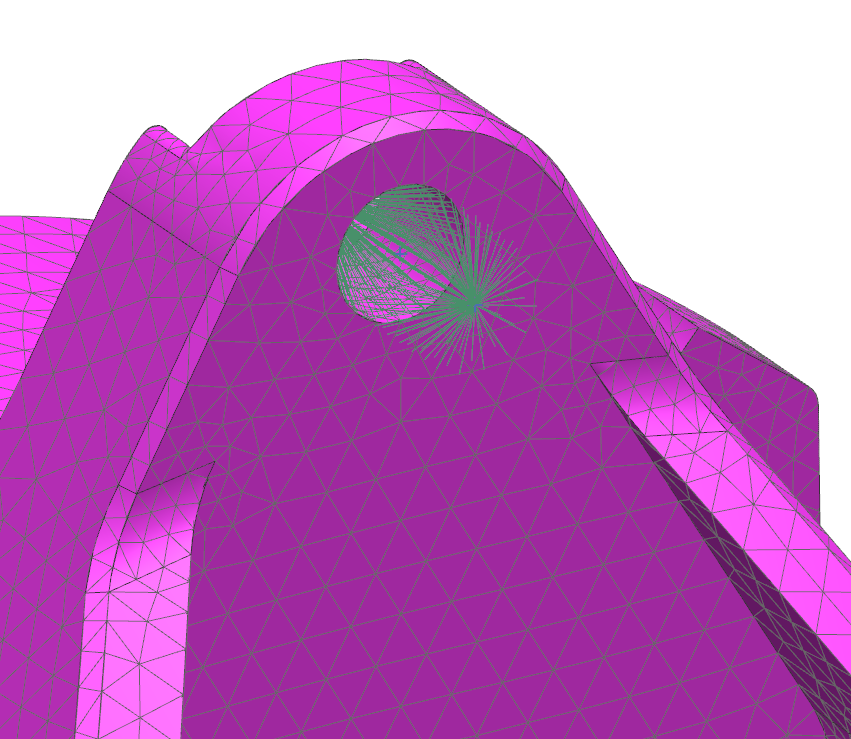
Next, I moved on to meshing and setting up the model. I started in 1D, with CBUSH elements being used to simulate bolts as well as bearings, with an RBE3 element at each end to distribute their loads. I also used an RBE3 element to connect a point representing the tire's contact patch to the simplified rim's face.
For 2D, I used a Manual Coincident Mesh Mate to "glue" the bearings and ring gear to the Hub and Carrier, simulating the press-fit they'd have in real life.
Finally, I meshed the geometry in 3d. More complex geometry was meshed with CTETRA(10) second-order elements, while simpler geometries such as the ring gear and bearings were meshed using CHEXA(20) swept elements.
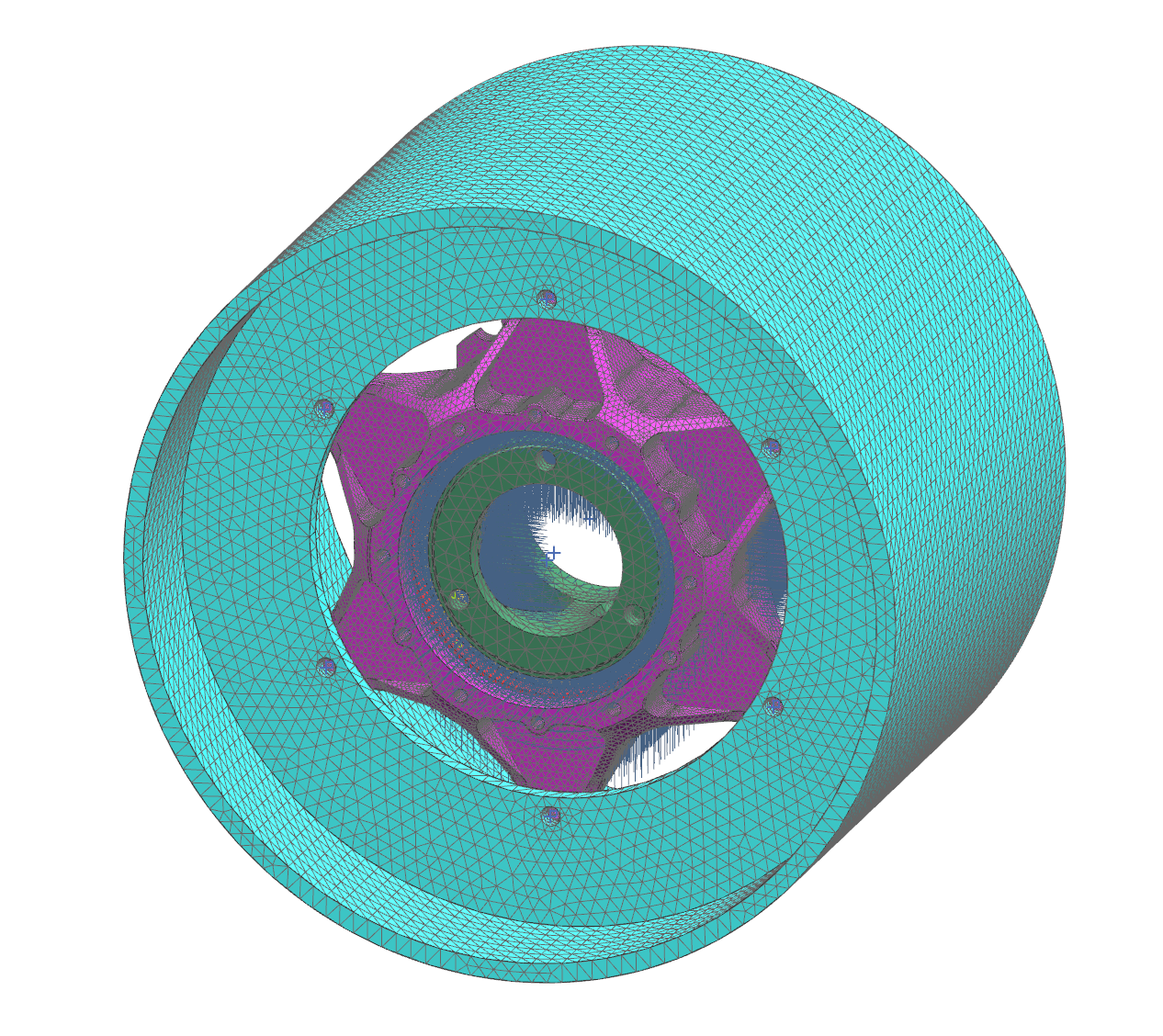
Next, I set up my constraints, in this case fixing the rear face of the carrier as well as fixing the rotational axes of the ring gear. I first set up a Modal analysis, which tells me what vibrational modes the system has. This allows me to verify I've constrained the hub properly. Additionally, it's a design requirement that the Hub's first mode is above 42Hz, which is the frequency of the wheel turning.
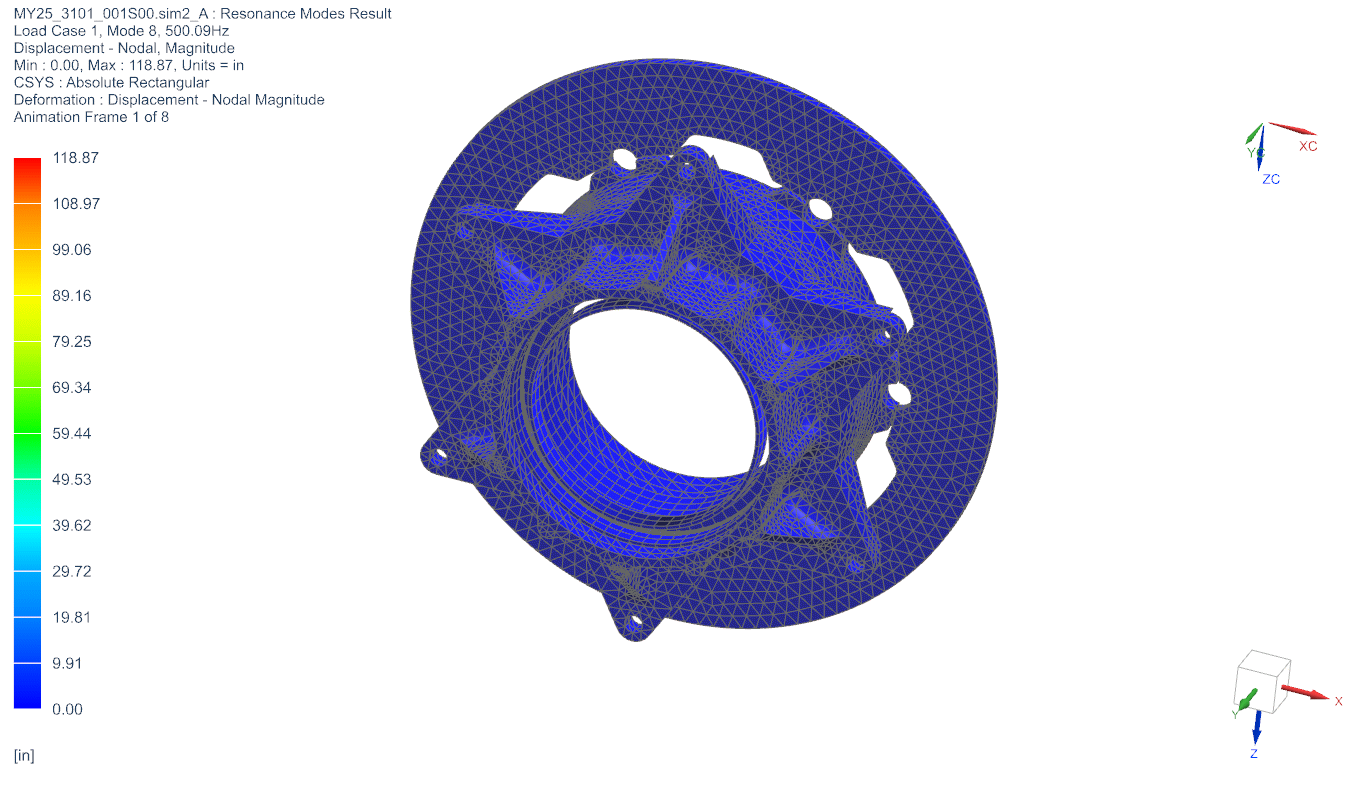
An example of an early modal analysis: in this case the outboard bearing was not properly constrained.
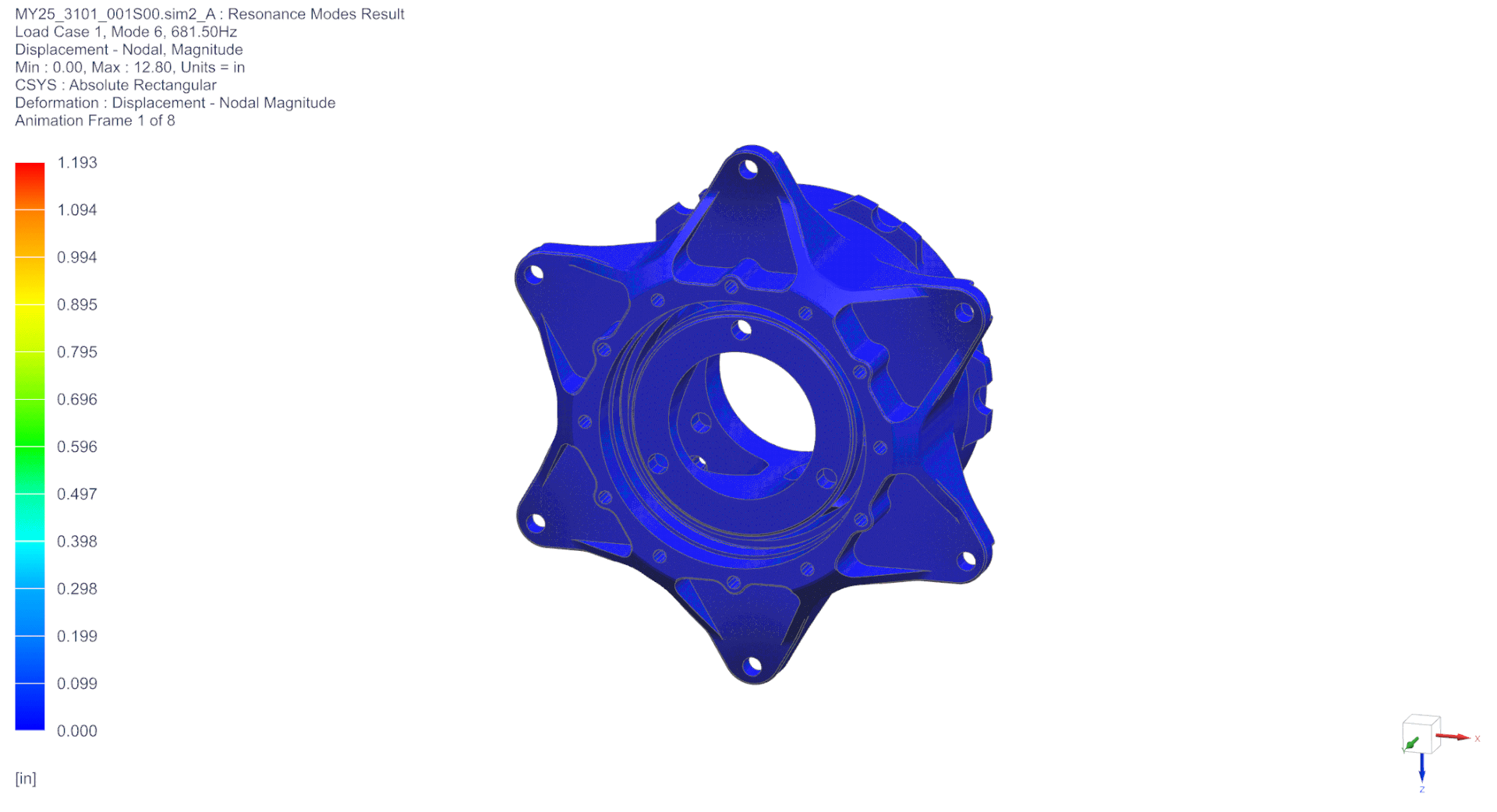
A properly constrained mode. My first mode was ~330 Hz, far above the design requirement.
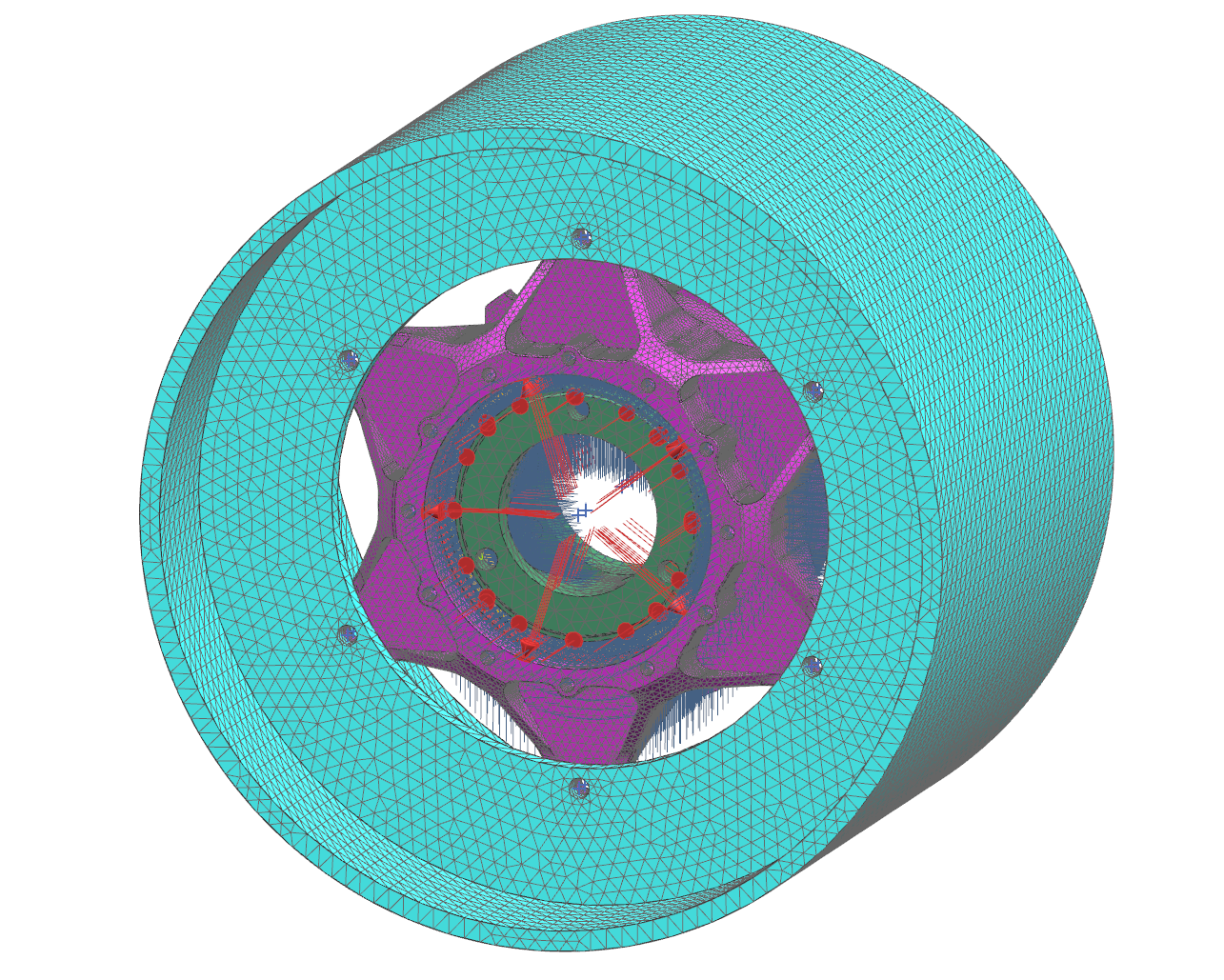
Next, I moved on to deflection analysis. I set up forces representing the bearing and ring press fits, the bearing preload, and the loads the hub experiences at max cornering, which is the worst load it experiences.
The Deflection result. As expected, the top and bottom tabs experience the most bending loads. Overall Camber/wheel angle deflection ends up being 0.4 degrees at 3000 N cornering, well within our deflection budget.
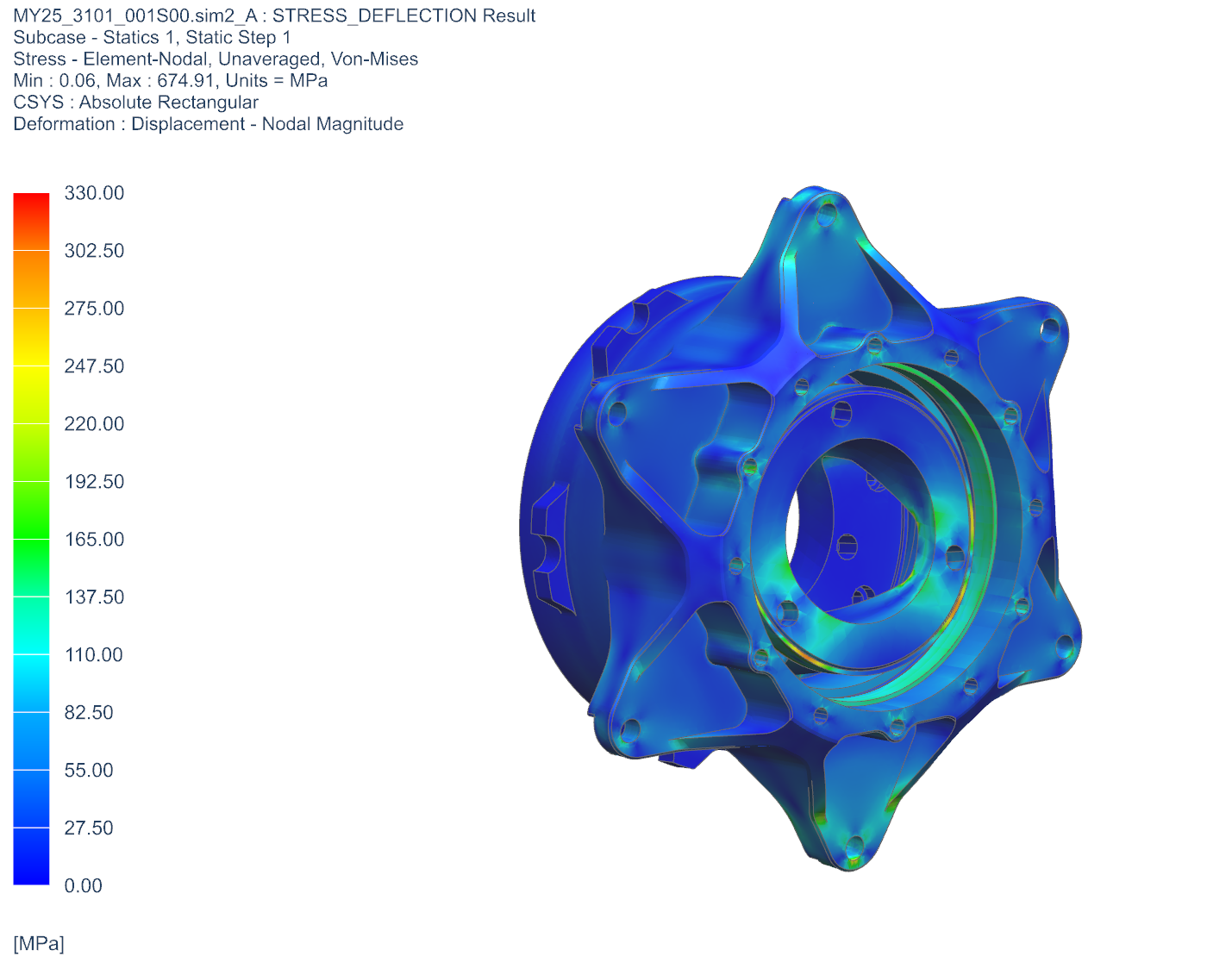
Stress results. No part of the hub is close to yielding. Typically I'd want to be as close to a 1.5 factor of safety (330 MPa) as possible, however, due to the large diameter and shortness of the hub, I hit manufacturing constraints preventing me from optimizing further.
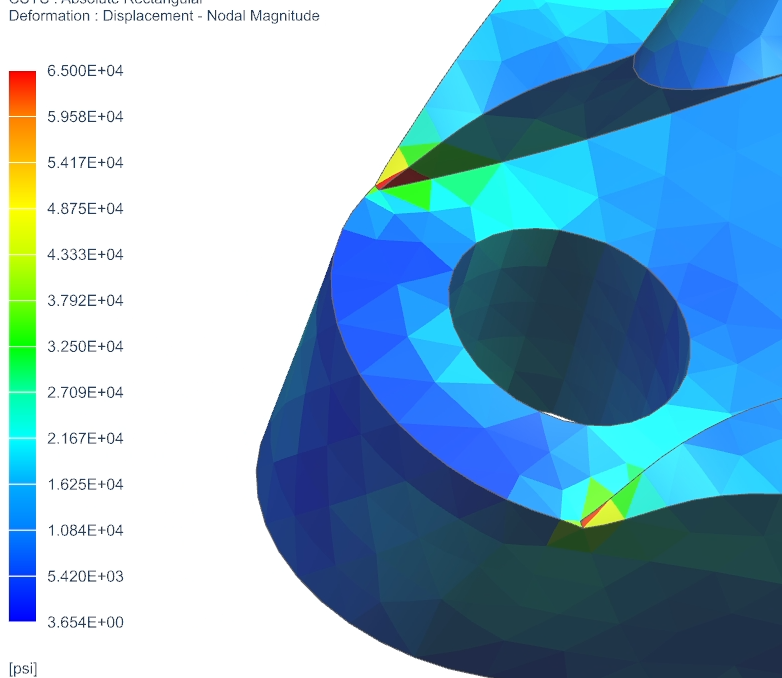
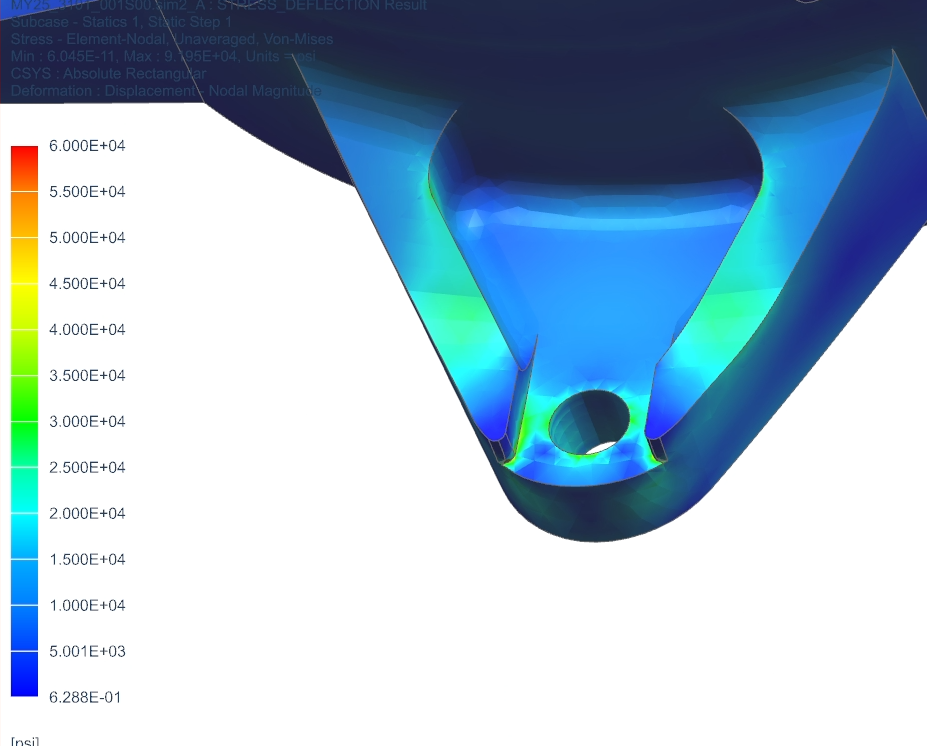
The FEA helped me discover a stress concentration at the hex head capture geometry. To fix this, I made the tab wider, reducing the sharp corner that caused the stress concentration.