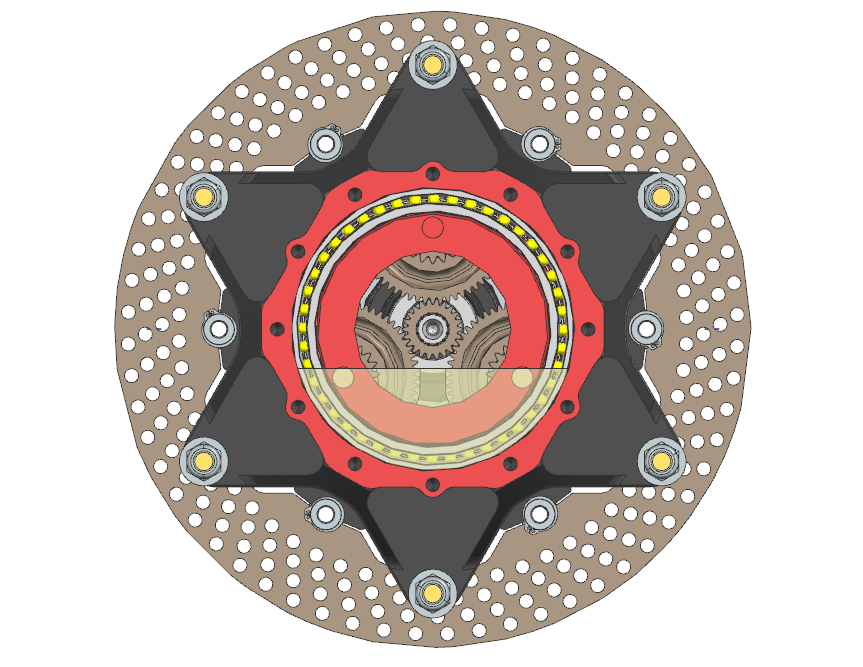
The MY25 Wheel Hub In the main assembly.
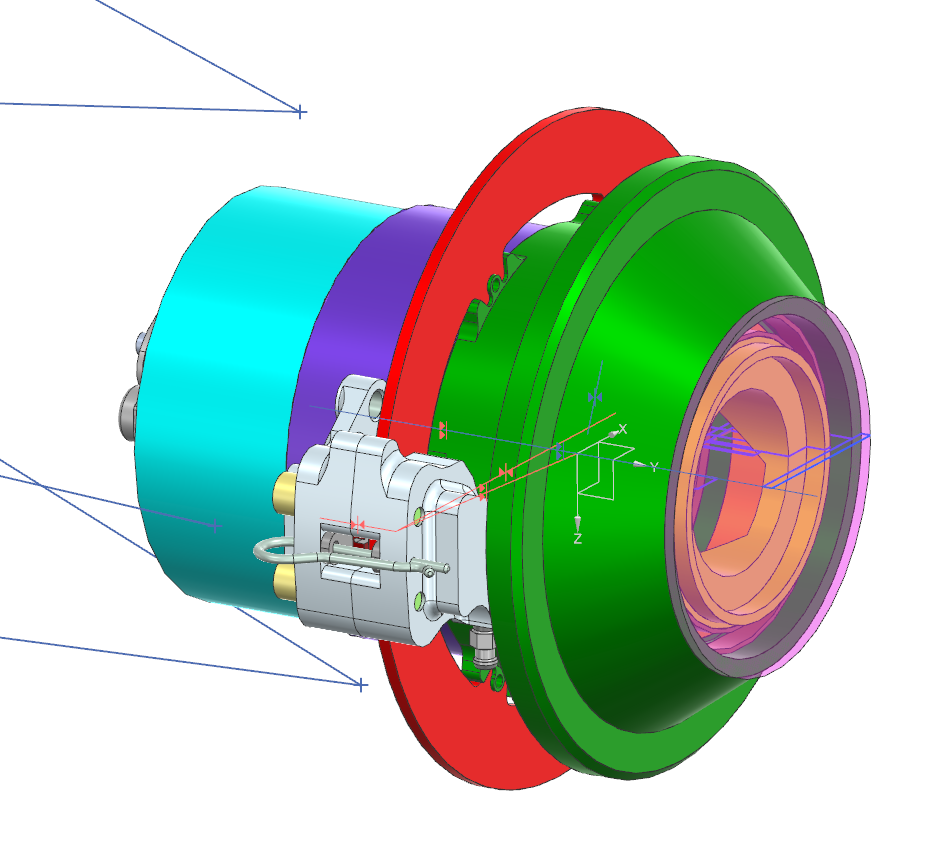
As always, we start off with a wheel package space fill to determine where we can add geometry.
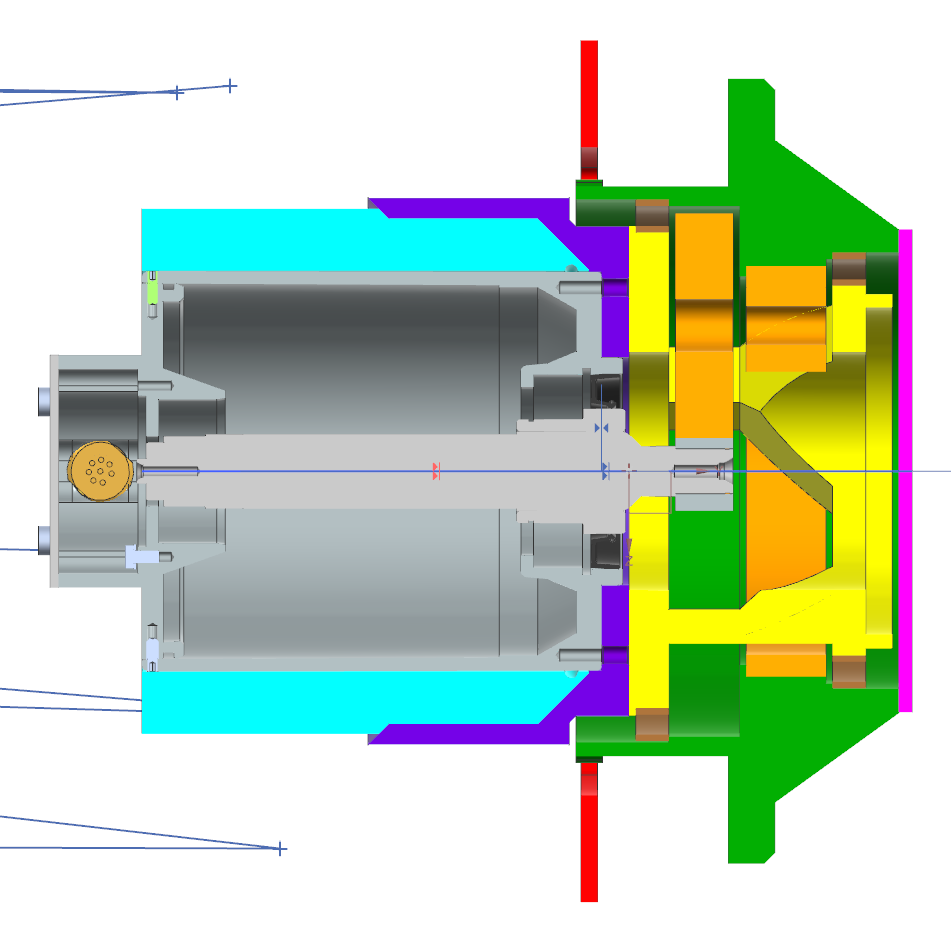
This year, we're pursing in hub gearboxes to enable four wheel drive, so my hub must fully enclose and seal the gearbox off from the outside.
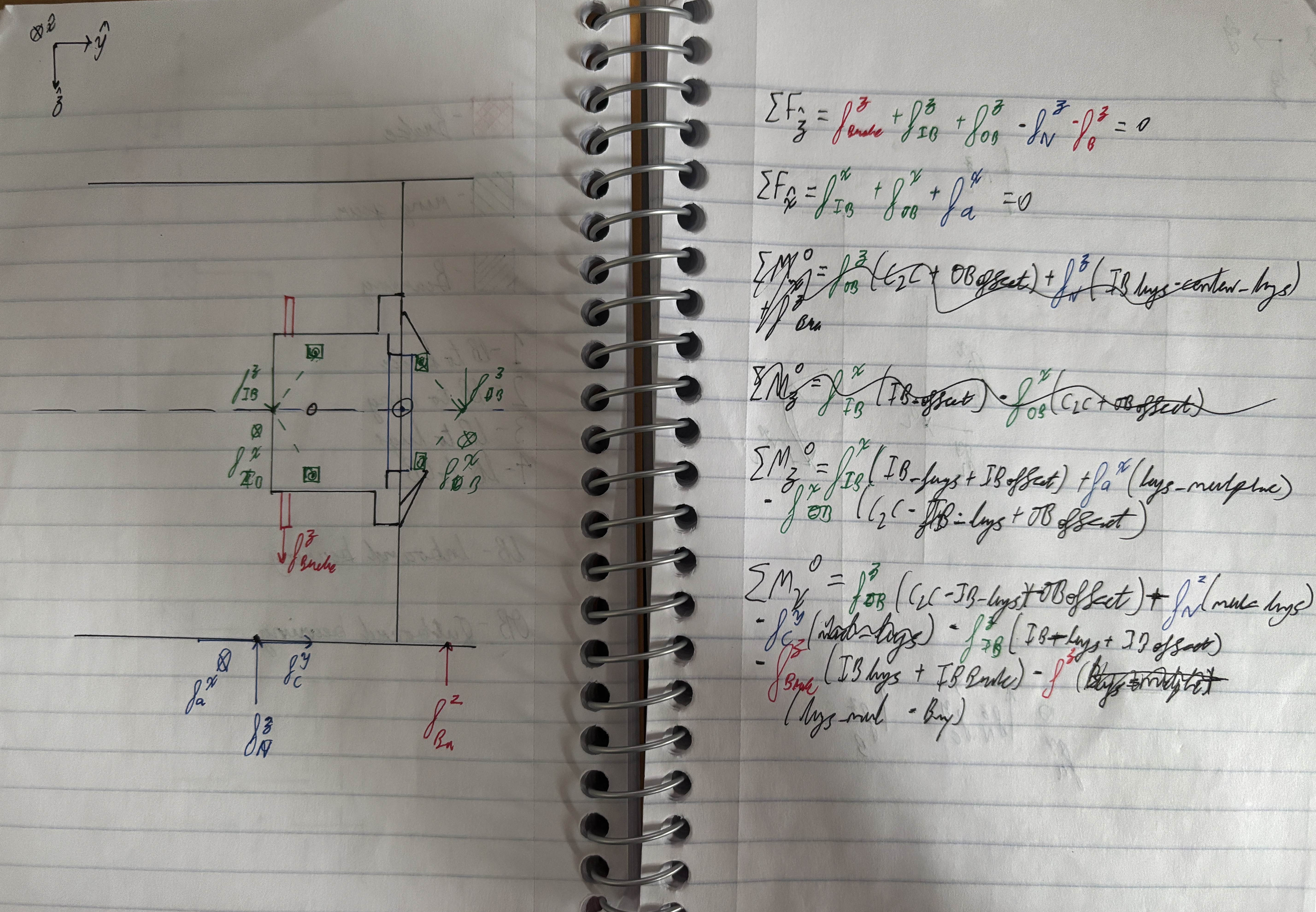
Once I had an idea of what the hub would look like, I moved onto drawing free body diagrams to derive the bearing and lug reaction forces from the contact patch forces.
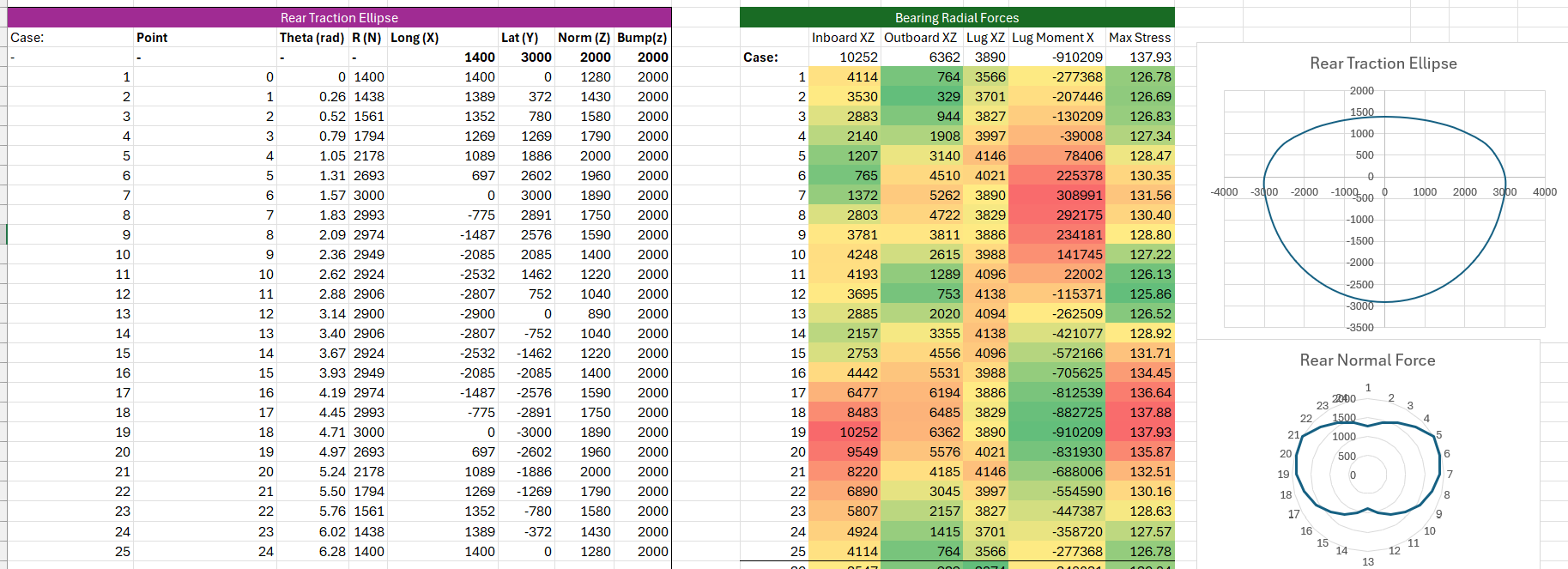
I conducted a sweep across our traction ellipse in order to determine my driving load case, which ended up being maximum steady state cornering.
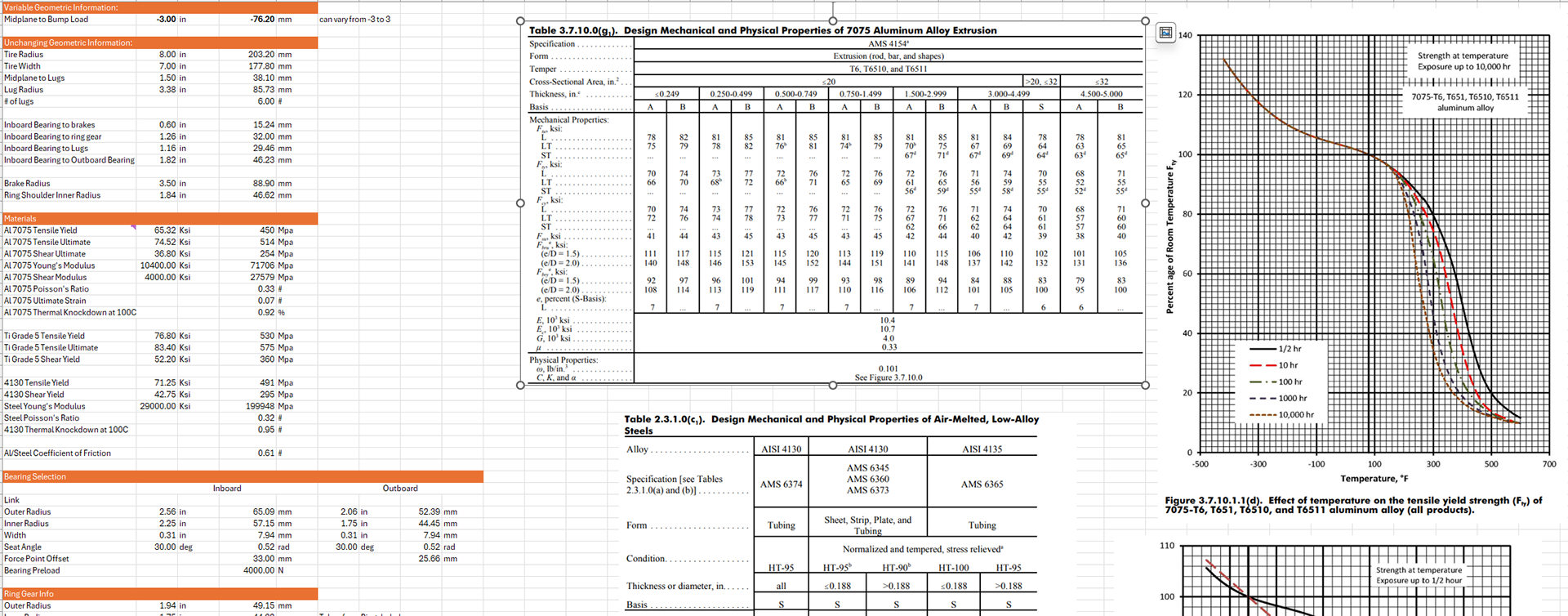
I then move on to determining my constraints. I knew that I would end up using Aluminum 7075-T6 as it has the best strength to weight ratio of any easily machinable material. However, I know that the gearbox will reach temperatures up to 100 degrees Celsius, so I have to apply a thermal knockdown as Al 7075 weakens with long exposure to high temperatures.
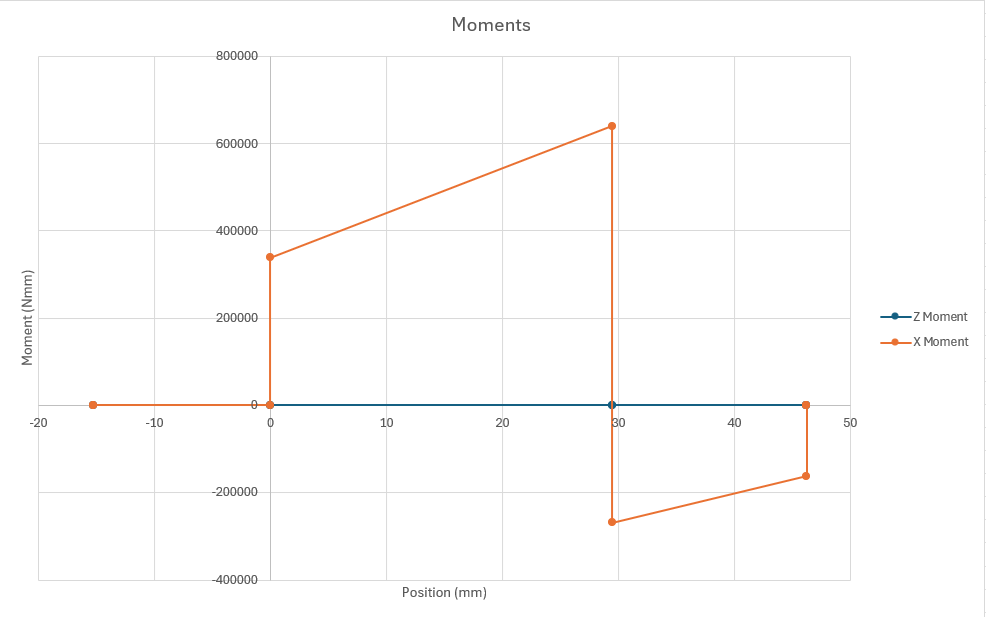
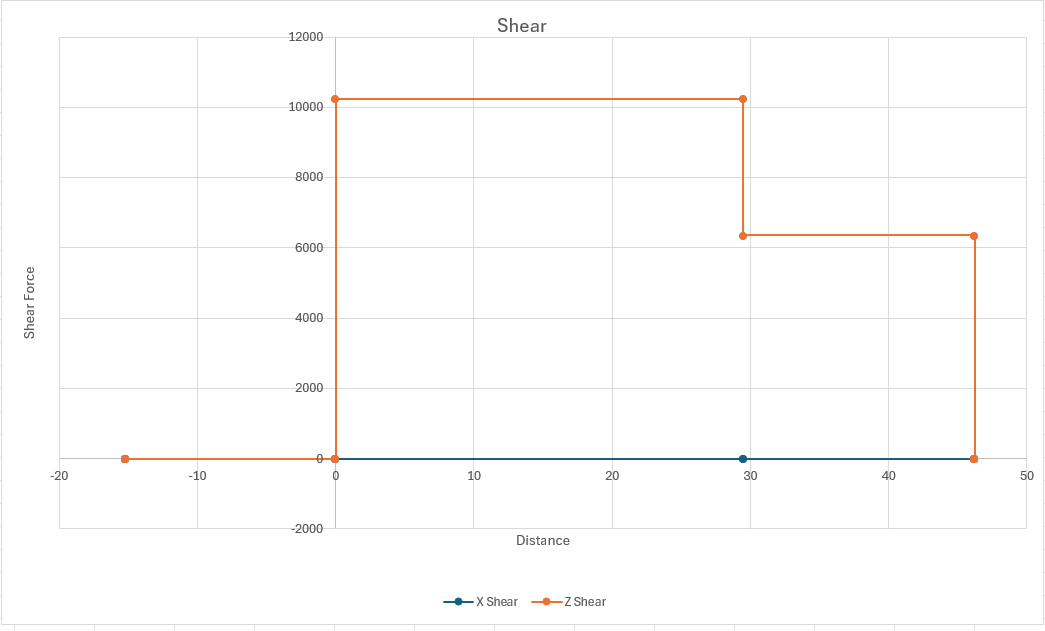
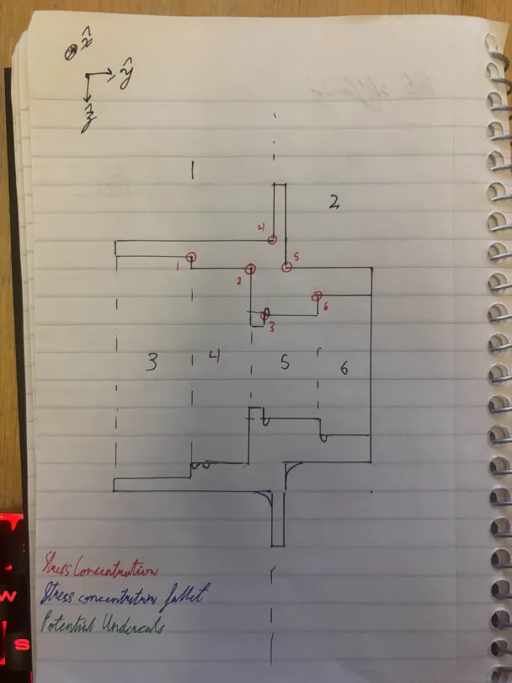
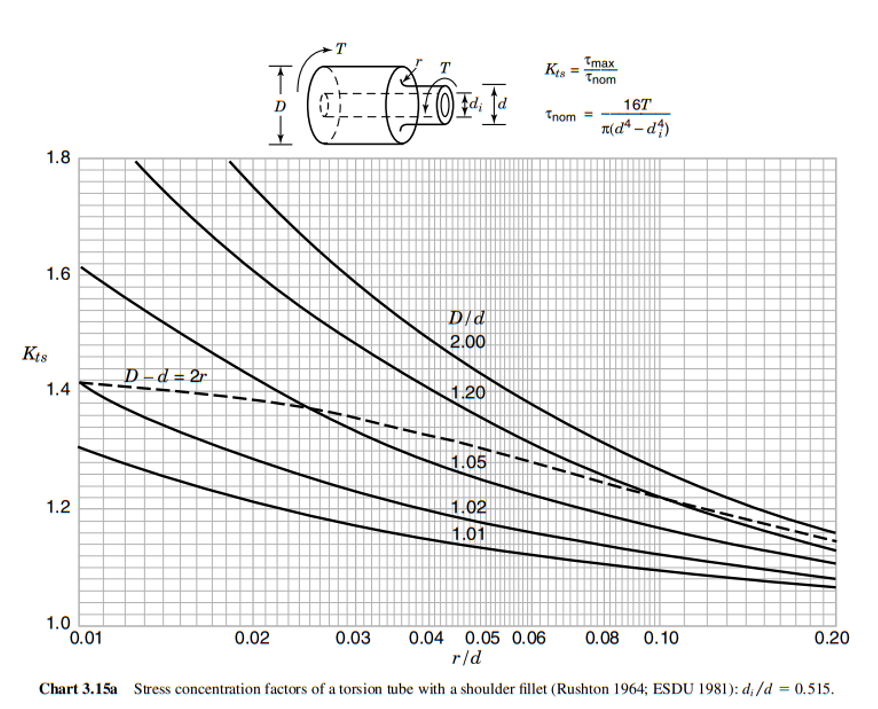
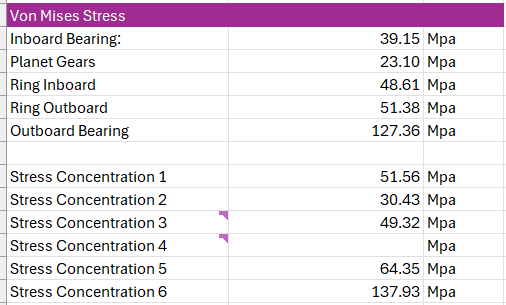
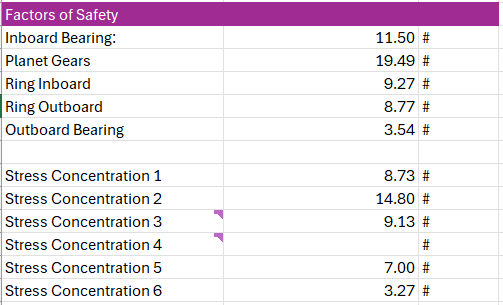
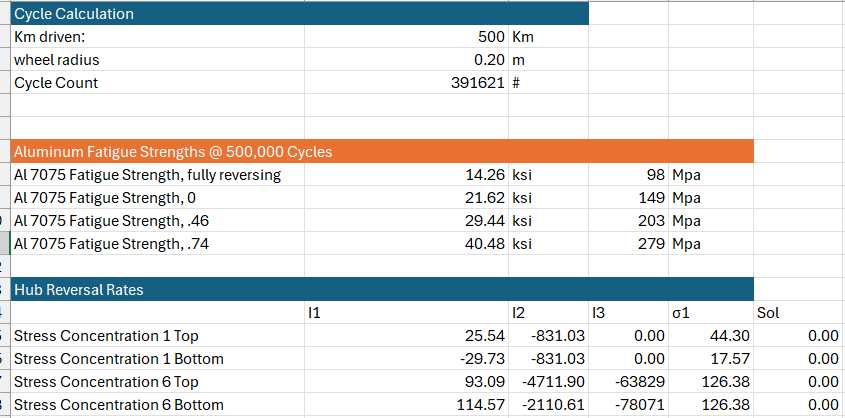
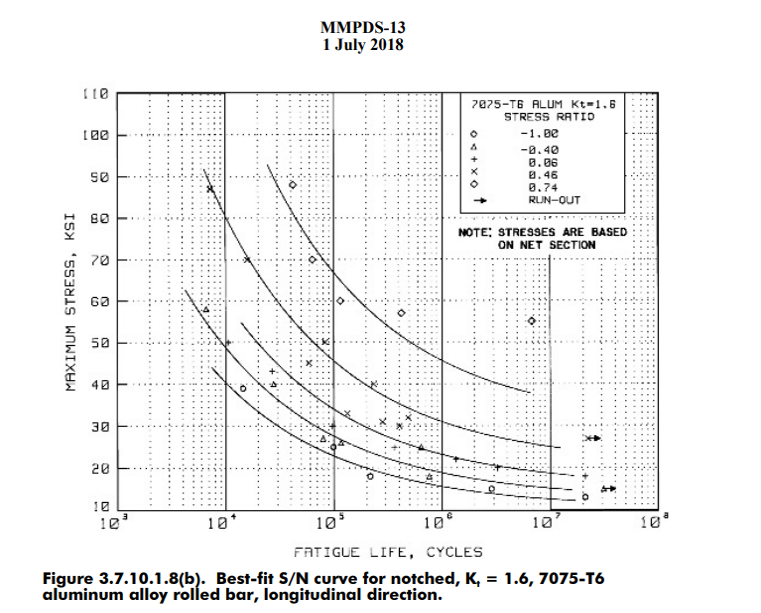

My next step was to CAD. I created the model using Siemens NX.
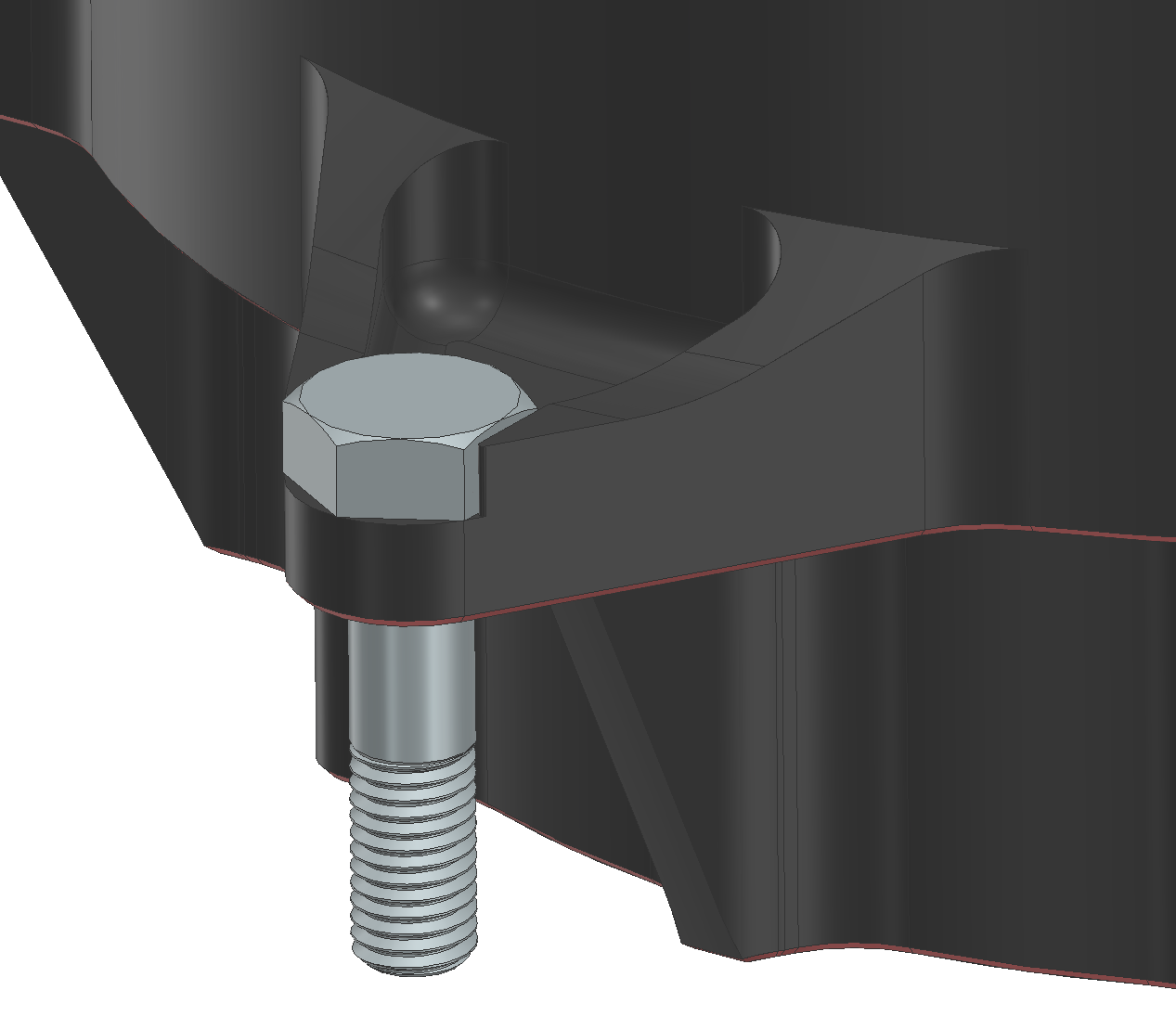
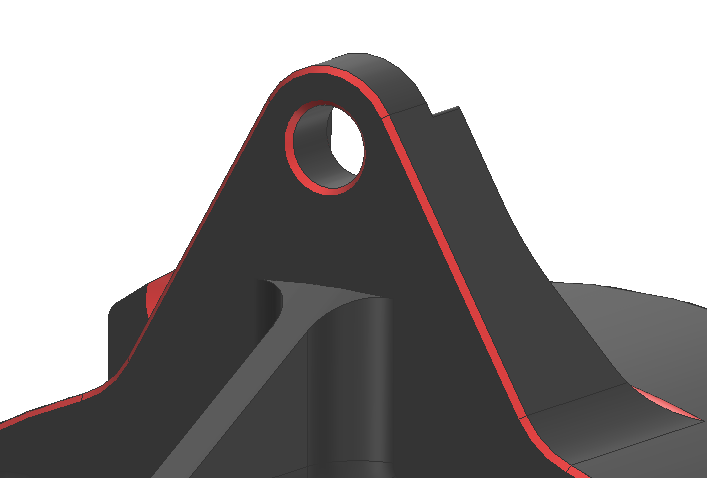
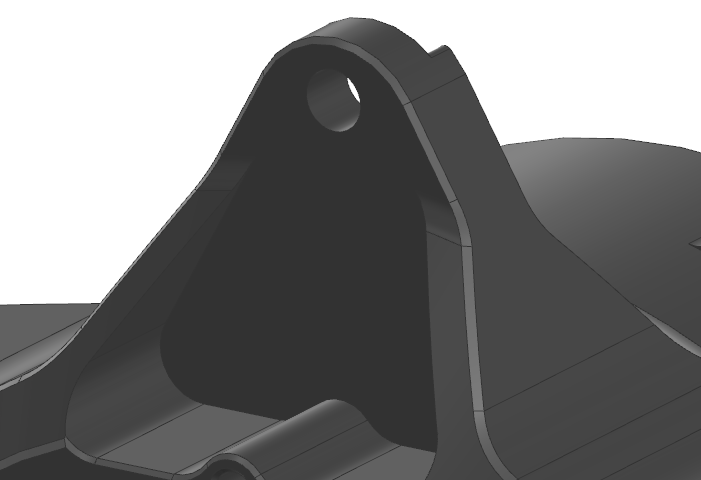
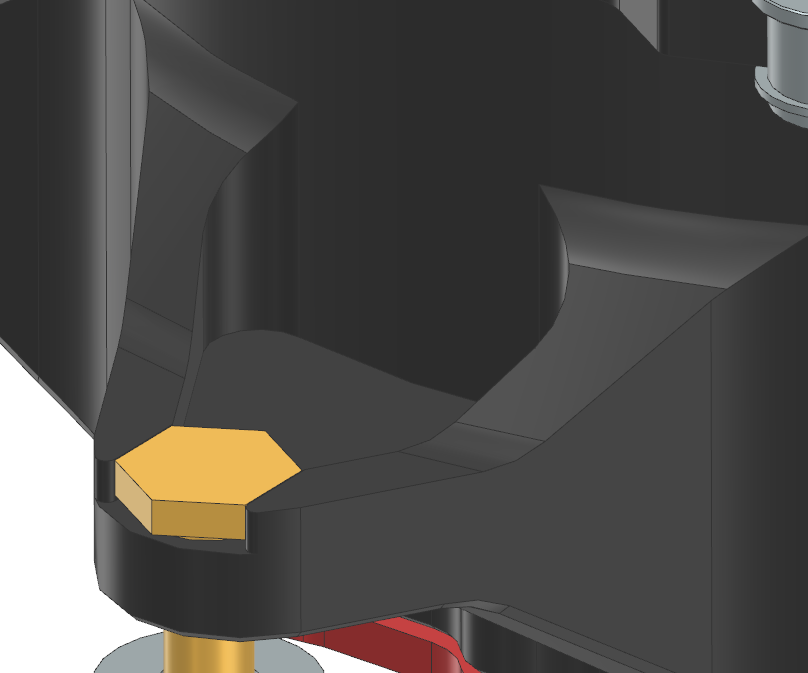