To enable four-wheel drive, we needed a compact way to reduce the speed of our motor. To do so, we researched different options and eventually utilized Kisssoft AG to size and design our gearbox.
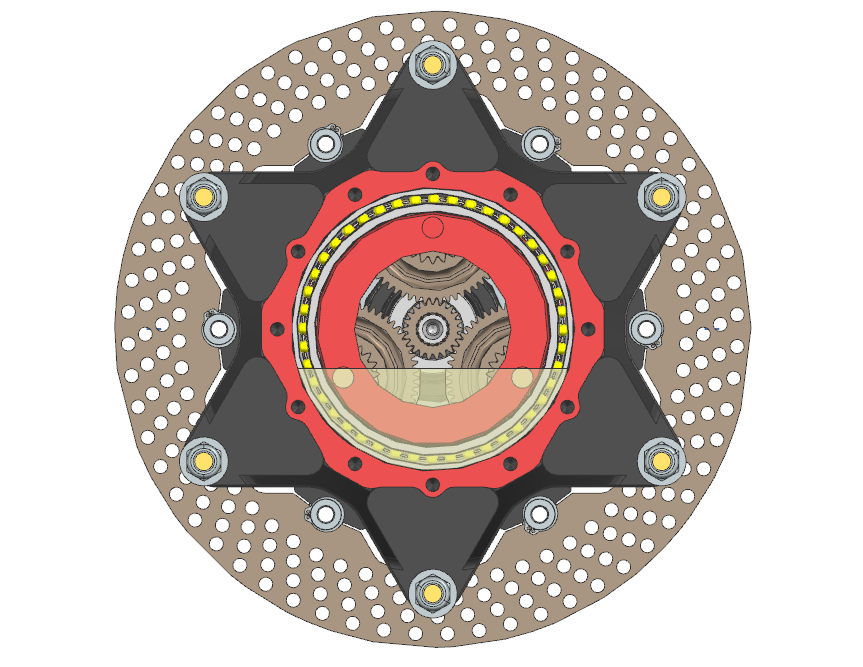
The final gearbox inside of the hub.
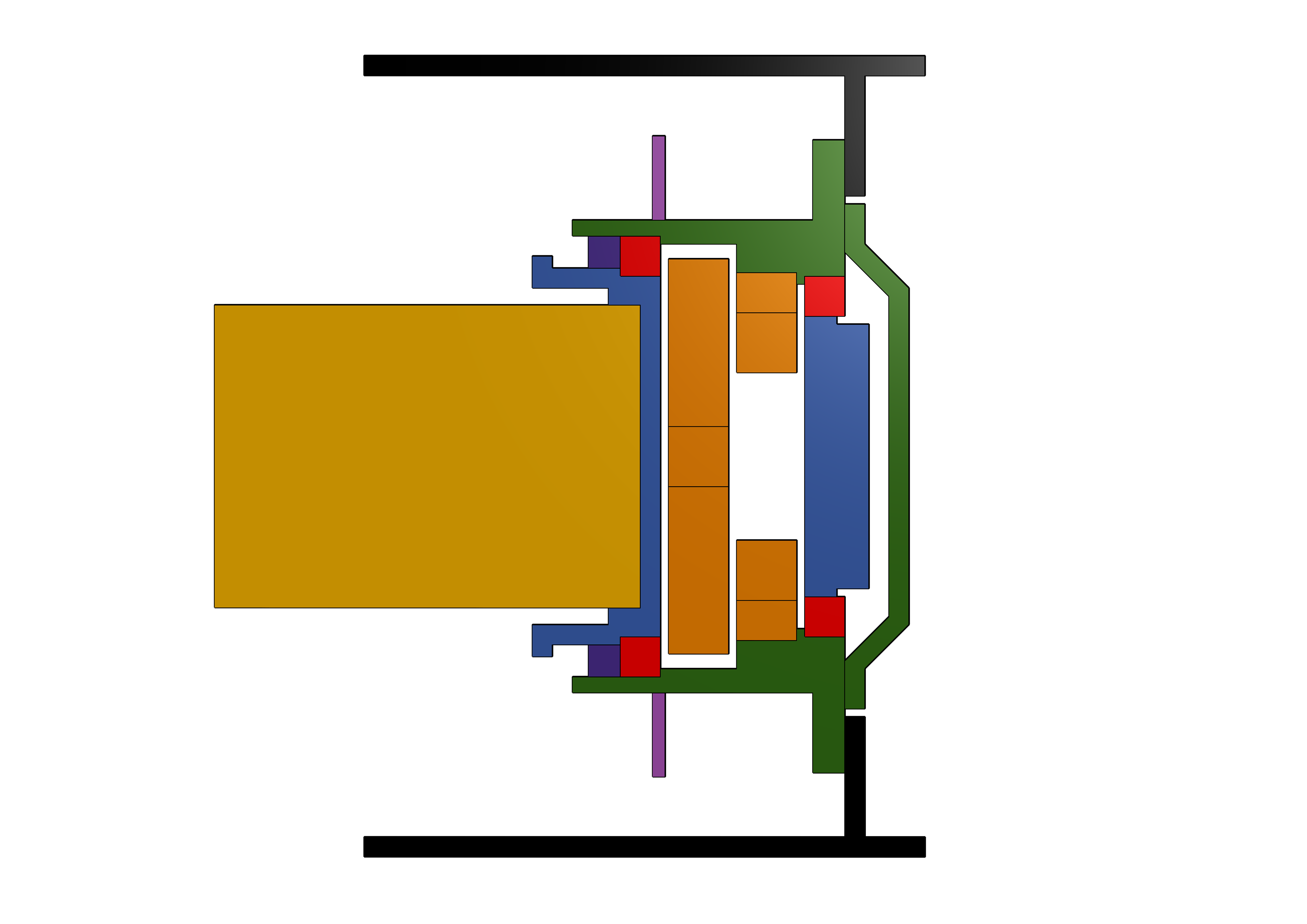
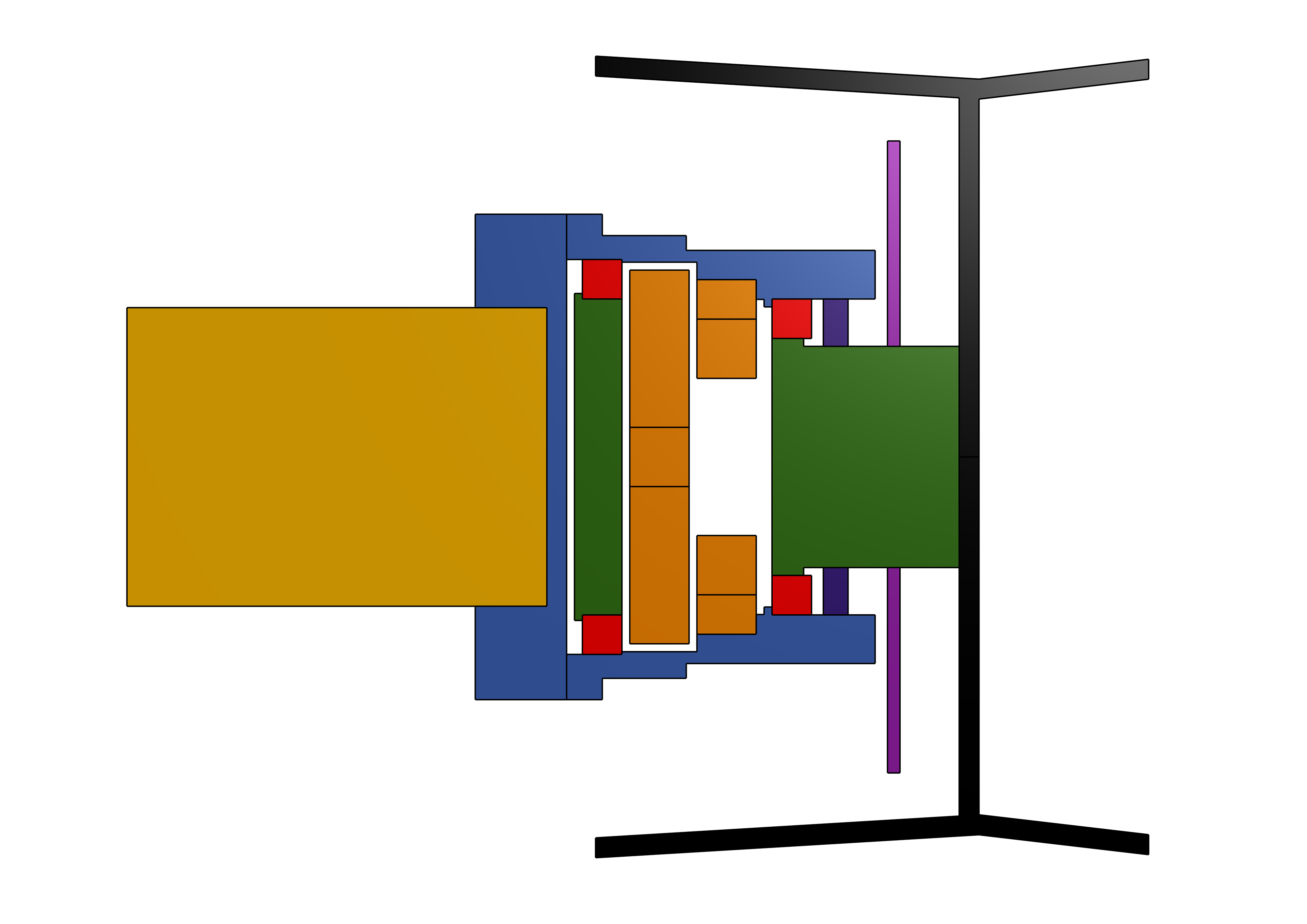
We first started off with choosing an architecture. After deciding on around a 12:1 reduction, we decided on a compound epicyclic gearbox. The issue was, that could mean a star gearbox, where the ring gear rotates, or a planetary, where the planets and carriers rotate while the ring gear stays static. We mocked both up and decided on a star setup due to simpler suspension packaging and a smaller polar moment of inertia. Our decision slides can be found here.
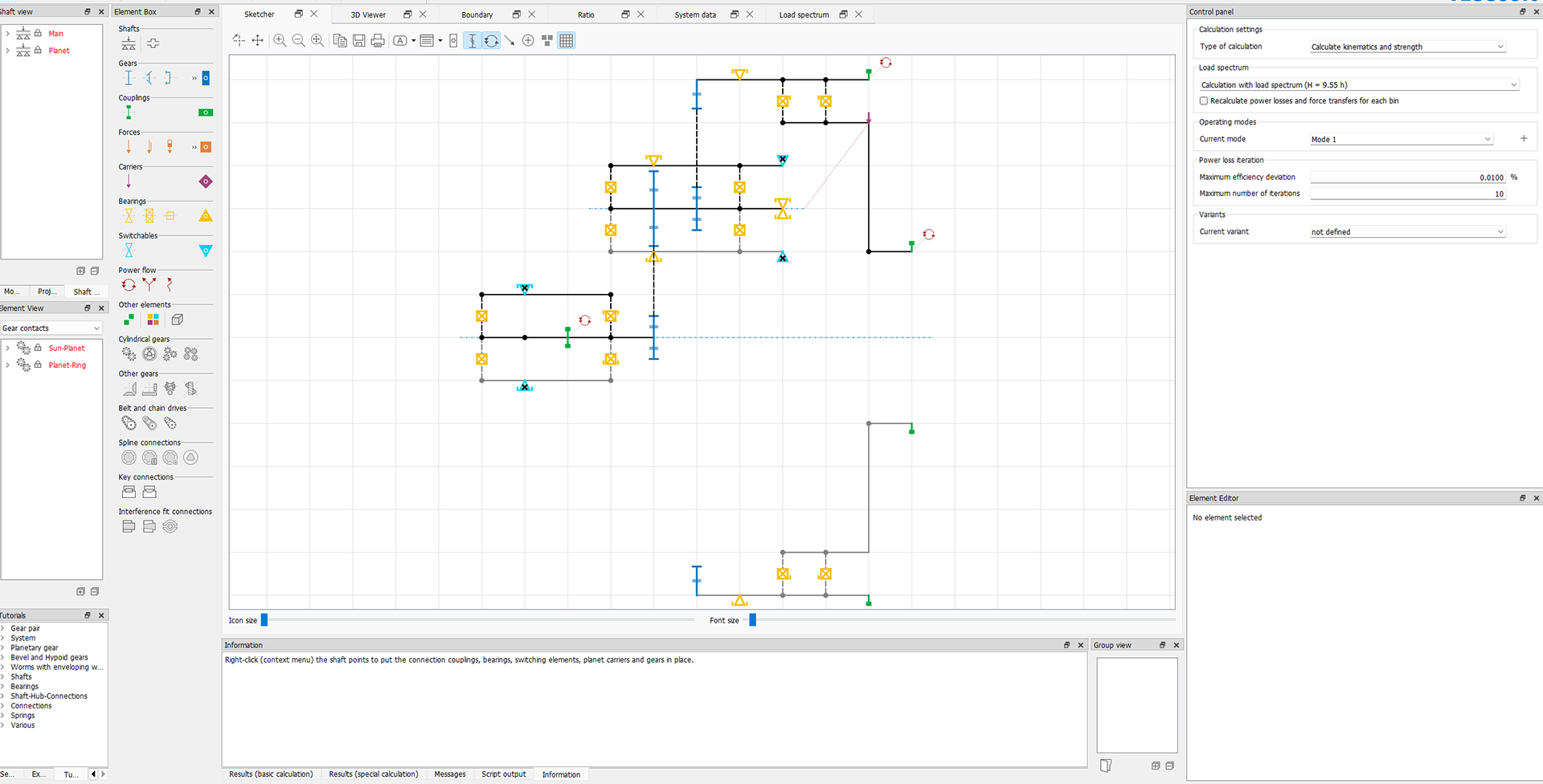
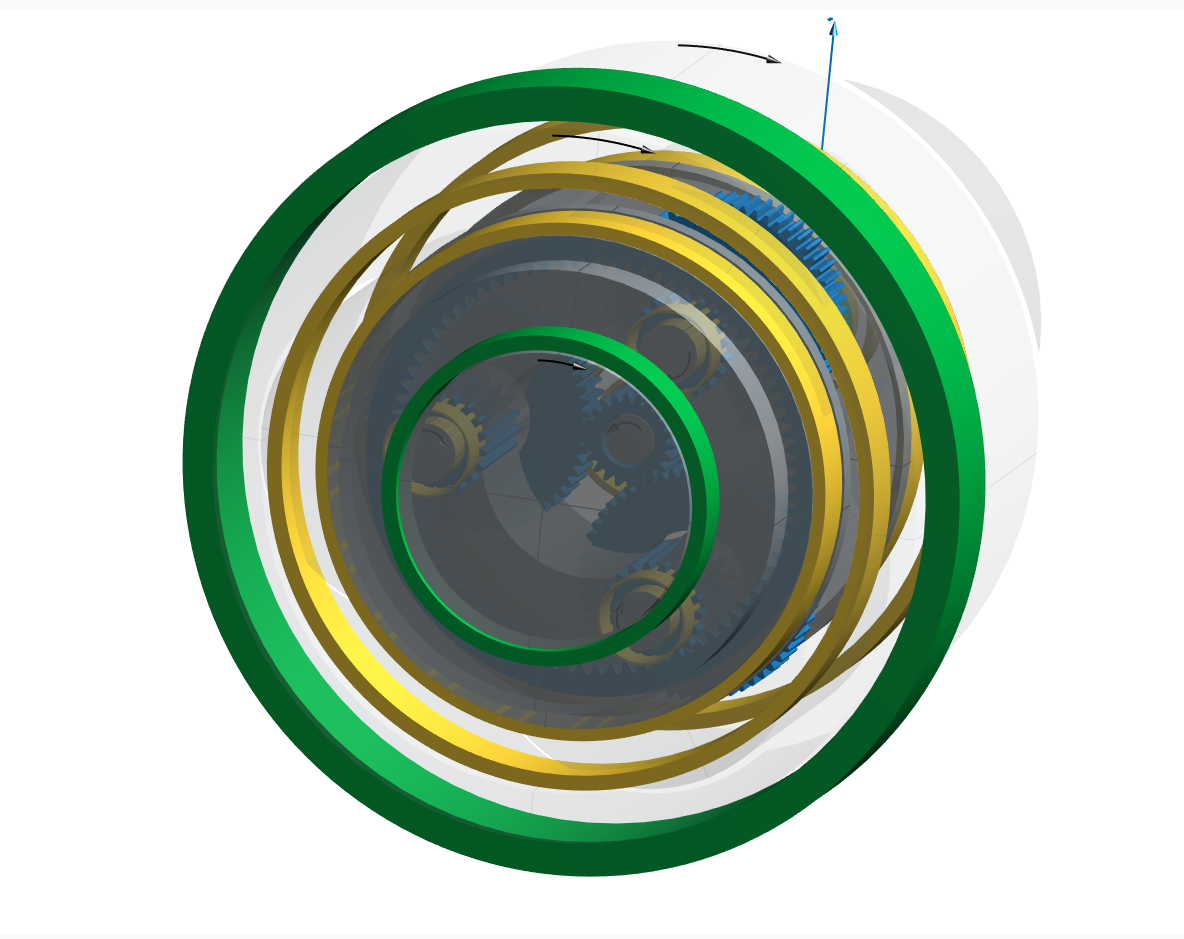
Once we read through the AGMA 6123 "Design Manual for Enclosed Epicyclic Gear Drives" and the ISO 6336 Standard, we moved on to sizing our gearbox in Kisssoft AG using a compound planetary gearbox template. We used our lap simulator to get an idea of what load spectrum the gearbox will experience.
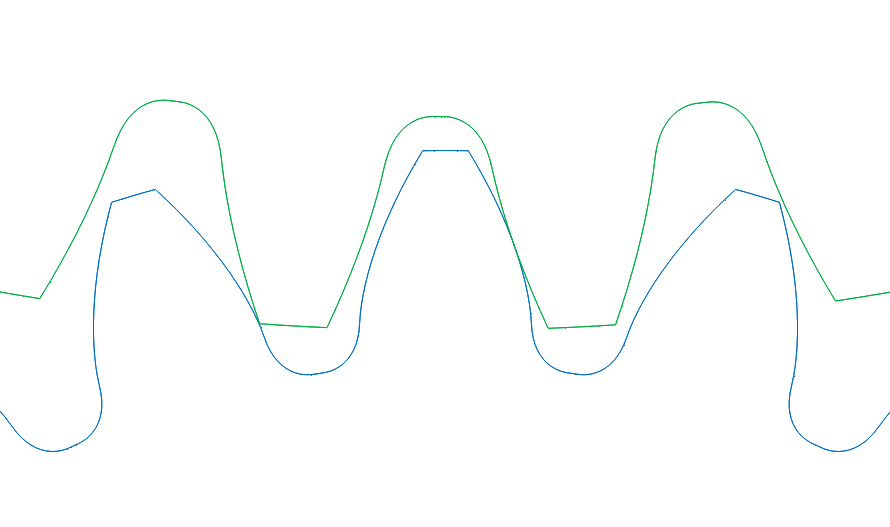
As we planned on conducting regenerative breaking, we knew that high fatigue loads would be placed upon our gears. We also knew there would be shock loads from bumps, and that the planetary setup could not perfectly divide the load by 3. We accounted for this using different factors that went into Kissoft.
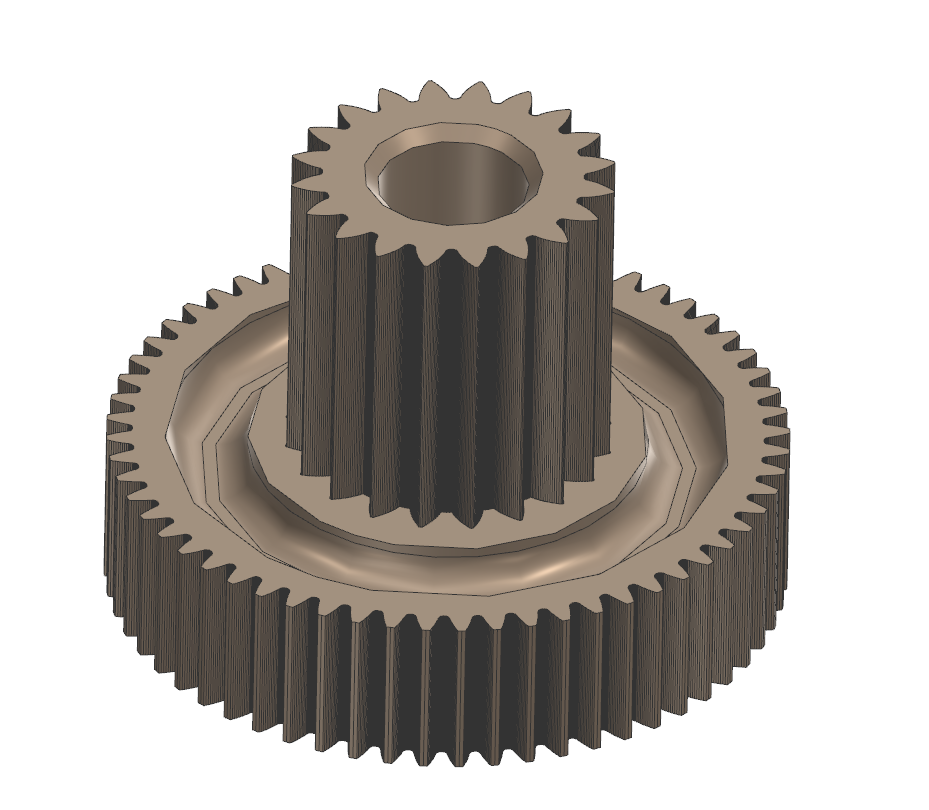
To connect the planets, we elected to continue the profile of the smaller planet gear and use it as a spline to link to the larger planet. We also created a pocket to reduce the weight of the gears.
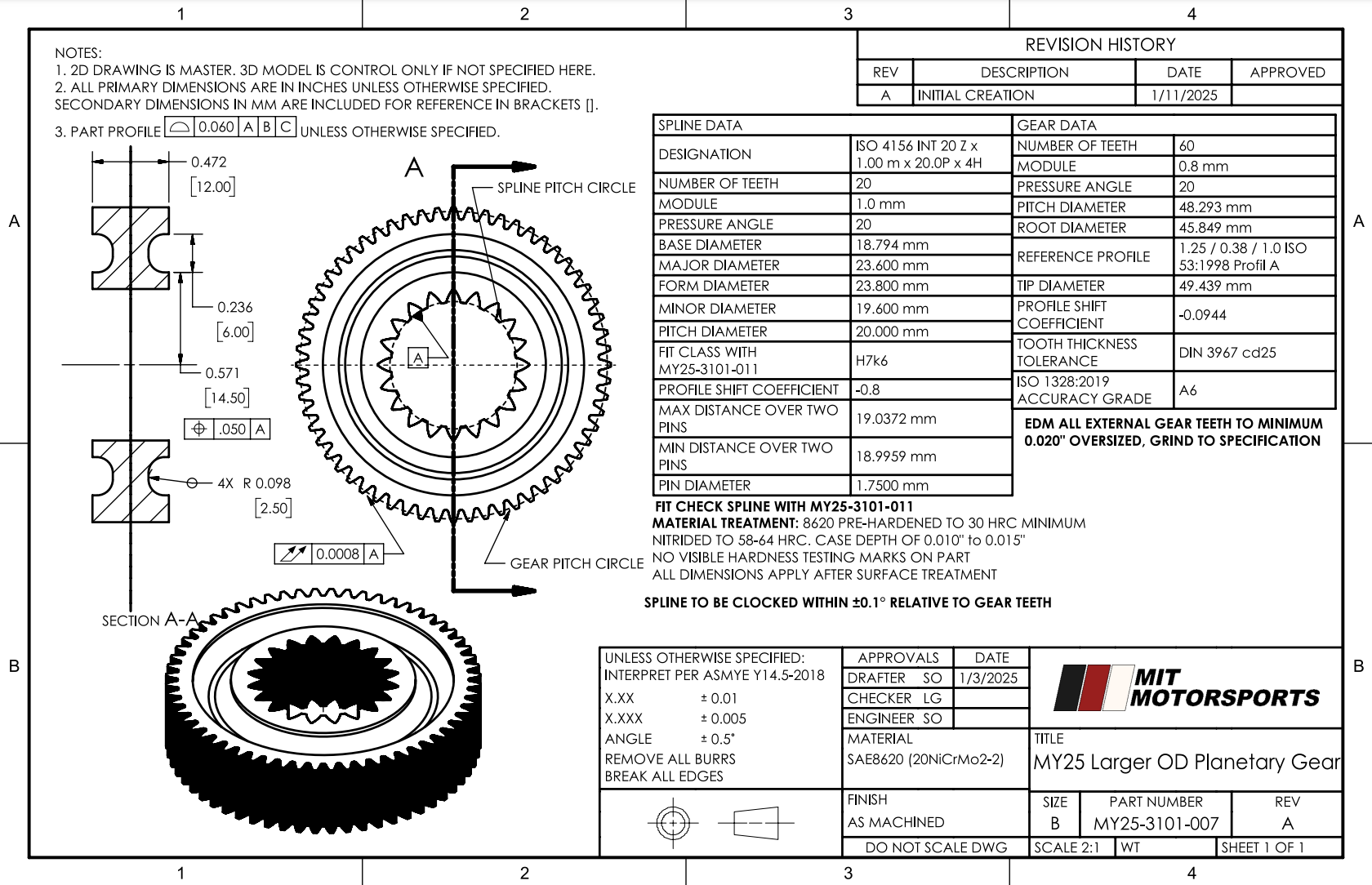
As we lacked the manufacturing capability necessary to EDM and grind these gears ourselves, I prepared drawings to send out. We decided on having the gears be made of 8620 Steel with a core hardness of 30HRC, nitrided to 59HRC to improve root and flank safety. We decided on nitriding instead of carburizing our gears due to previous bad experiences with carburization warping our gears.